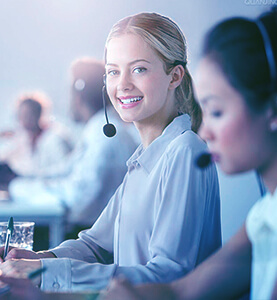
What is the Fuel for Industrial Boiler
In the industrial sector, boilers are extremely important pieces of equipment, widely used in food processing, chemical production, textiles and many other industries, undertaking the crucial task of providing heat and steam for processes such as cooking, drying, sterilizing and distilling. However, have you ever thought about what types of fuels are used in industrial boilers? And how do these fuels affect the performance and application of the boiler?
Different types of industrial boilers, such as the common fire-tube boilers, water-tube boilers, electric boilers, and biomass boilers, are each adapted to different fuels, which makes them uniquely suited for different industrial scenarios.
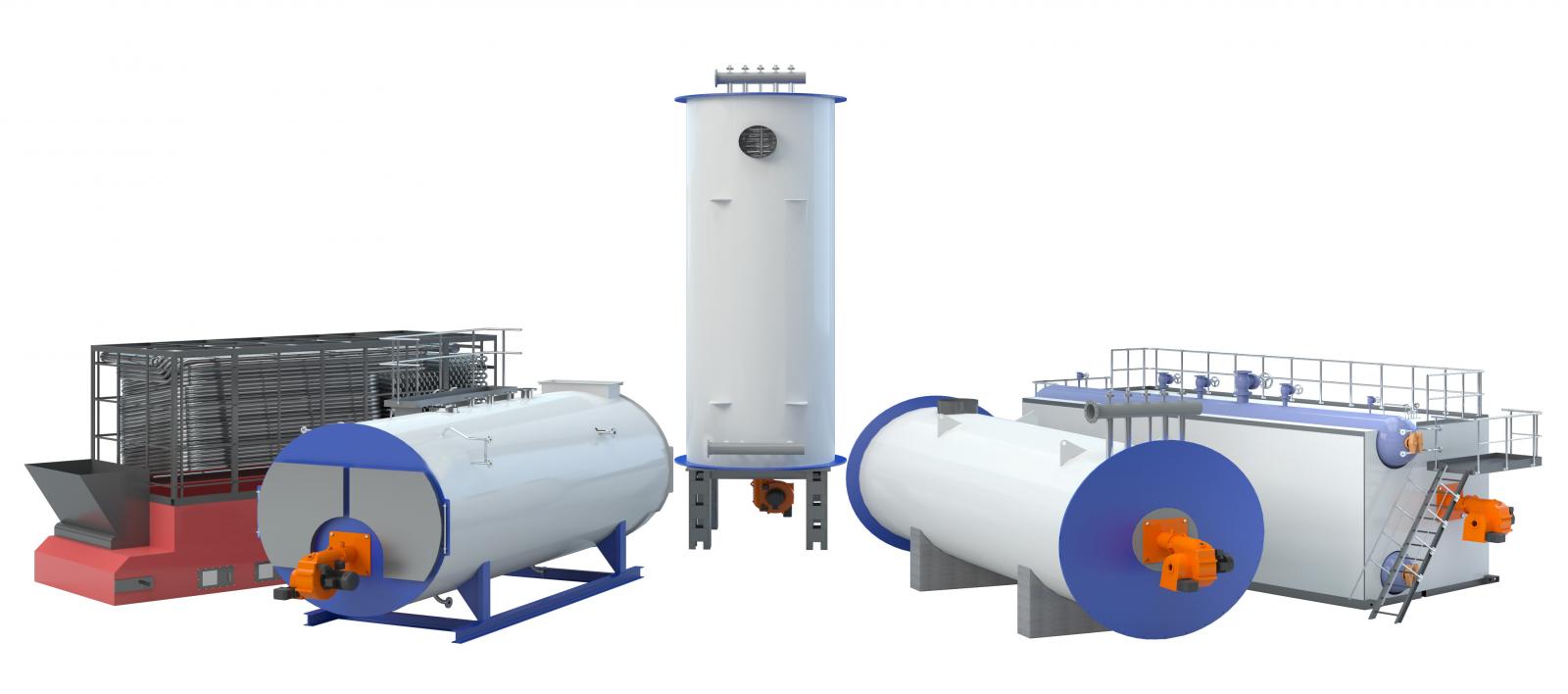
Types of Industrial Boiler Fuels
Gaseous fuels
Gaseous fuels mainly include natural gas, liquefied petroleum gas (LPG), coal gas and biogas. Of these, natural gas is the most widely used gaseous fuel. It is characterized by clean combustion, producing fewer pollutants during combustion, as well as a high thermal efficiency that efficiently converts chemical energy into heat. Natural gas is typically delivered to the point of use via pipeline, which greatly reduces the need for on-site storage and lowers storage risks and costs. LPG, gas and biogas are also used in specific scenarios.
For example, LPG may be used as an alternative fuel in some remote areas that do not have access to natural gas pipelines; gas is recycled as a by-product of some industrial processes; and biogas, which is often derived from the fermentation of organic waste, is a renewable energy option that may be used in some industrial facilities on farms or near sewage treatment plants.
Solid fuels
The main solid fuels are coal and biomass pellets. In the past, coal used to be the dominant fuel for industrial boilers. However, with increasingly stringent environmental protection policies, traditional coal-fired boilers are difficult to meet environmental targets due to their high pollutant emissions, and many small coal-fired boilers have been banned from use.
Biomass pellets are environmentally friendly solid fuels that have emerged in recent years. It is processed from straw, peanut shells and other agricultural waste, with the advantages of energy saving, emission reduction, combustion process produces relatively less pollution. Moreover, compared with coal, the cost of biomass pellets may be lower, which makes it a more ideal alternative to coal-fired boilers.
Liquid fuels
Liquid fuels include methanol, light oil and heavy oil. Oil-fueled boilers are similar in structure to gas-fired boilers, but the burners are different, as oil-fired boilers use oil burners. In some areas where natural gas pipelines have not yet been laid, oil-fired boilers have become an important heating option.
Different liquid fuels have different characteristics. For example, light oil has relatively high combustion efficiency and fast startup, which is suitable for industrial scenarios with more rapid response to heating demand; while heavy oil has high energy density, but its combustion process may require more complex treatment to ensure full combustion and reduce pollutant emissions.
New Energy Fuel - Electricity
Electricity, as a new energy fuel, is also used in industrial boilers, i.e. electrically heated boilers. The electric heating boiler absorbs electrical energy through the internal electric heating components and converts it into heat energy to produce steam or hot water.
This type of boiler is characterized by intelligent operation, and parameters such as temperature and pressure can be precisely adjusted through an automated control system. At the same time, it is safe, produces no open flames or exhaust emissions during operation, and has a relatively high thermal efficiency.
However, the main disadvantage of electrically heated boilers is their high operating cost, which makes their application in some areas with high electricity costs somewhat limited, and they are usually more suitable for small industrial facilities or specific production processes that have very high environmental requirements, limited space and are not too sensitive to operating costs.
Factors to Consider Before Choosing a Boiler Fuel
Boiler Fuel Cost
Fuel cost is a significant part of the operating cost of an industrial boiler and is influenced by a number of factors, not least of which is geographic location. In Bangladesh, the reference figures are as follows
Cost Comparison Table (1-Ton Boiler) |
|||||
No. |
Fuel |
Fuel Consumption/Hr |
Cost of Fuel (TK/Unit) |
Total Cost/Hr (TK) |
Cost to Produce per kg of Steam (TK/kg) |
1 |
Natural Gas |
75 m³ |
10.7 (per m³) |
802.5 |
0.80 |
2 |
CNG |
28 kg |
43.5 (per kg) |
1218 |
1.22 |
3 |
Diesel |
60 L |
68 (per L) |
4080 |
4.08 |
4 |
Charcoal (Rice Husk) |
200 kg |
12 (per kg) |
2400 |
2.40 |
5 |
Wood |
220 kg |
8 (per kg) |
1760 |
1.76 |
6 |
Coal |
90 kg |
22 (per kg) |
1980 |
1.98 |
Ease of use and safety
Fuel type largely determines the ease of use and safety of a boiler. Propane and natural gas are extremely volatile. In the event of a leak in the piping or boiler, to avoid danger, personnel must immediately evacuate the site and hire a professional for repairs.
In contrast, fuel oil and coal are much more stable. Even if a fuel leak occurs, it does not pose much of a safety threat to personnel who do not have specialized repair skills.
Coal is also the most stable of all fossil fuels, with virtually no risk of explosion, a hazard inherent in gaseous fuels. The stability of the fuel not only affects safety in use, but also the ease of maintenance. Stable fuels make simple repairs easier to carry out, thus saving time and costs.
Boiler life for a given fuel type
Of the 1, 2 and 3 ton boilers, gas and oil-fired boilers usually have a relatively small initial fixed investment. In terms of service life, gas-fired boilers typically last up to 20 years, which is the longer service life of all types of boilers. This is due to the fact that natural gas burns cleaner, produces fewer impurities, and causes relatively less corrosion and wear and tear on the internal components of the boiler.
Some solid fuels, such as coal, contain more impurities and produce a large amount of ash during combustion, which may accumulate on the heating surface of the boiler, not only reducing the efficiency of heat transfer, but also leading to corrosion of the equipment, thus shortening the service life of the boiler.
Comparison of Common Steam Boiler Fuels
In order to more intuitively understand the characteristics of different fuels, we compare common steam boiler fuels through the following table:
Fuel Type |
Efficiency |
Cost |
Emissions |
Maintenance |
Storage/Handling |
Availability |
Natural Gas |
High |
Medium |
Low |
Low |
Requires gas pipelines |
Widely available |
Coal |
Medium |
Low |
High |
High |
Requires storage silos |
Region-dependent |
Oil |
Medium |
High |
Medium |
Medium |
Requires fuel tanks |
Available but costly |
Biomass |
Variable |
Low - Medium |
Low |
High |
Requires storage |
Varies by region |
Electricity |
High |
High |
Zero (if from renewable sources) |
Low |
No storage needed |
Depends on grid power |
As you can see from the table, each fuel has its own unique advantages and limitations, and companies need to weigh their choices against their own realities.
Detailed Overview of Steam Boiler Fuel Selection
Natural Gas
Natural gas is one of the most commonly used fuels for industrial boilers due to its high combustion efficiency and clean combustion process. During the combustion process, natural gas can be fully mixed with oxygen to achieve efficient combustion, producing fewer pollutants, such as sulfur dioxide, nitrogen oxides and particulate matter, which greatly reduces the impact on the environment.
At the same time, since natural gas produces almost no ash after combustion, it makes boiler maintenance relatively simple, reducing downtime and maintenance costs due to ash cleaning. In addition, its lower carbon emissions are in line with current global requirements for environmental protection, helping companies to achieve their sustainability goals.
Coal
Coal, as a traditional boiler fuel, has the advantage of low cost and relatively low price per unit of energy. This allows coal to be used in some large-scale industrial operations that are cost-sensitive and have a high demand for steam.
Due to the large amount of ash produced after combustion, boilers need to be cleaned regularly, which increases the workload and cost of maintenance. Therefore, coal is mainly suitable for large-scale industrial plants that are located in areas with abundant coal resources and can meet strict environmental emission control requirements.
Fuel Oil
Fuel oil, as a liquid fossil fuel, has a high energy content and can provide strong power for boilers, which is suitable for industrial applications that require high steam pressure. As a result, fuel oil is often used as a back-up fuel for industrial facilities that cannot rely on a steady supply of natural gas, or as a temporary replacement in specific situations where other fuel supplies are in question.
Biomass
Biomass fuels, such as wood chips, agricultural waste and pellets, are renewable and sustainable. The use of biomass fuels can significantly reduce a company's carbon footprint and is in line with the concept of environmental protection and sustainability.
In some regions with abundant agricultural resources, the use of local agricultural waste to produce biomass pellets as boiler fuel achieves resource utilization of waste and reduces the dependence on traditional fossil fuels.
In addition, biomass fuels require large storage space and their availability may be limited by seasonal and regional agricultural production.
Electricity
Electrically heated boilers that use renewable energy sources to generate electricity during operation are able to achieve true zero emissions and are extremely friendly to the environment. At the same time, electric boilers have low maintenance requirements as they do not have complex combustion systems and wearable parts. However, the cost of electricity is relatively high, especially in some areas where power resources are tight or electricity prices are high, and the operating costs of using an electric heating boiler can put greater financial pressure on a company.
Influence of Fuel on Boiler Performance
Efficiency and calorific value
The type and quality of fuel is a key factor in determining the thermal efficiency of a boiler. Thermal efficiency refers to the proportion of the chemical energy of the fuel that the boiler converts into useful heat energy. Different fuels have different calorific values, which is the amount of heat released per unit mass or volume of fuel when it is completely burned.
Combustion Characteristics
The combustion characteristics of the fuel include ignition temperature, combustion rate and flame stability. These characteristics directly affect the combustion effect of the fuel in the boiler combustion chamber.
For example, some fuels have a low ignition temperature, can be quickly ignited at a low temperature, and the combustion rate is moderate, flame stability, which is conducive to the realization of efficient and stable combustion process. Some fuels, on the other hand, may have less desirable combustion characteristics, such as too fast or too slow combustion rates, unstable flames, and a tendency to flame out or incomplete combustion. Incomplete combustion will lead to fuel waste, increase pollutant emissions, and also reduce the thermal efficiency of the boiler.
Therefore, understanding the combustion characteristics of fuels and optimizing the boiler's combustion system based on these characteristics is critical to improving boiler performance.
Emissions and environmental impact
Different fuels produce different amounts and types of pollutants, such as sulfur dioxide, nitrogen oxides, carbon dioxide, and particulate matter, during the combustion process. These pollutants have a negative impact on the environment and human health.
For example, natural gas burns relatively cleanly and produces fewer pollutants, and its carbon emissions are also lower, which has less impact on the environment. Coal combustion, on the other hand, releases a large amount of pollutants, especially sulfur dioxide and particulate matter, which are one of the main sources of air pollution.
Maintenance and operational life
The choice of fuel has a significant impact on the maintenance needs and operational life of the boiler. Some fuels containing impurities, such as sulfur and ash in coal, can form deposits on the heat exchange surfaces of the boiler during combustion, and these deposits can reduce the efficiency of heat transfer and lead to energy waste.
At the same time, impurities may also trigger corrosion, damaging the metal parts of the boiler and increasing maintenance costs and downtime. Long-term use of such fuels can shorten the overall operating life of the boiler.
On the contrary, the use of cleaner fuels, such as natural gas, reduces the problems of deposits and corrosion, reduces maintenance frequency, and extends the life of the boiler.
Therefore, from the perspective of long-term operating costs and equipment investment, choosing the right fuel is critical to ensuring stable boiler operation and extended service life.
Cost impact
Fuel cost is a major component of the operating cost of industrial boilers. Although some high-quality fuels, such as natural gas, may have a higher purchase price, the overall cost may be more favorable in the long run due to their high combustion efficiency and low maintenance requirements.
Some low-cost fuels, such as coal, on the other hand, may have low procurement costs, but due to their low combustion efficiency and high emissions, requiring additional investment in environmental protection equipment and frequent maintenance, the total cost may not be low in the end.
Therefore, when choosing fuels, enterprises need to consider the procurement cost, combustion efficiency, maintenance cost and environmental protection cost of the fuels in order to realize the optimal economic benefits.
Flexibility and availability
Fuel availability varies from region to region, which affects the practical application of industrial boiler systems. For example, in some remote areas, there may be a lack of natural gas pipeline infrastructure, limiting the availability of natural gas, while in coal-rich areas, coal is relatively easy to obtain.
In addition, some industries may wish to have the flexibility to use multiple fuels in their boilers so that adjustments can be made in the event of fuel price fluctuations or supply problems. For example, some boilers can be designed to run on natural gas as well as switch to fuel oil when necessary, and this flexibility can help companies respond to changes in the marketplace, safeguard continuity of production, and reduce operational risk.
Conclusion
The choice of fuel for an industrial boiler is a complex decision-making process involving a number of factors such as fuel type, cost, ease of use, safety, boiler life and environmental impact.
Different fuels have their own characteristics and applicable scenarios, and enterprises need to make the most suitable choice by weighing various factors according to the actual situation of fuel resources, environmental protection requirements, production scale and cost budget in their own regions.
At the same time, with the increasing awareness of environmental protection and the continuous development of energy technology, the future of industrial boiler fuels may appear more innovation and change in the field, such as the development and application of new biofuels, more efficient energy conversion technology, etc., the enterprise should pay close attention to these trends, in order to adjust the fuel strategy in a timely manner, to adapt to the needs of the industry development.