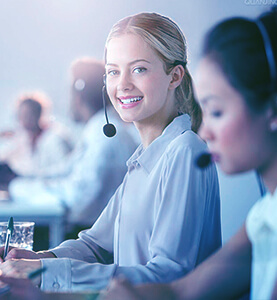
What is Boiler?
Behind our daily life and industrial production, there is a silent but vital equipment - boilers. From bringing warmth to thousands of households in cold winter days to serving as a source of power for industrial production, boilers are ubiquitous and have a profound impact on every aspect of our lives. This article will explore the mysteries of the boiler, from its definition, working mechanism, to the internal components, diverse types and a wide range of applications, to bring you an in-depth understanding of the industry and life in the “hero behind the scenes”.
Definition of Boiler
From a professional point of view, a boiler is a closed container. In this container, water or other liquids are heated, which in turn produces steam or water vapor, and the steam may be further overheated. The entire process takes place under pressure or vacuum, and the energy generated is used outside the vessel, either from fuel combustion, electricity or nuclear energy.
For a better understanding, we can take a common household kettle as an analogy. When boiling water, the kettle converts electrical energy into heat through a heating element at the bottom, which warms the water in the kettle until steam is produced. Although the kettle and the true sense of the boiler in the size and functional complexity of a large gap, but the basic principle is similar, are heating the liquid to produce steam.
The Working Mechanism of Industrial Boilers
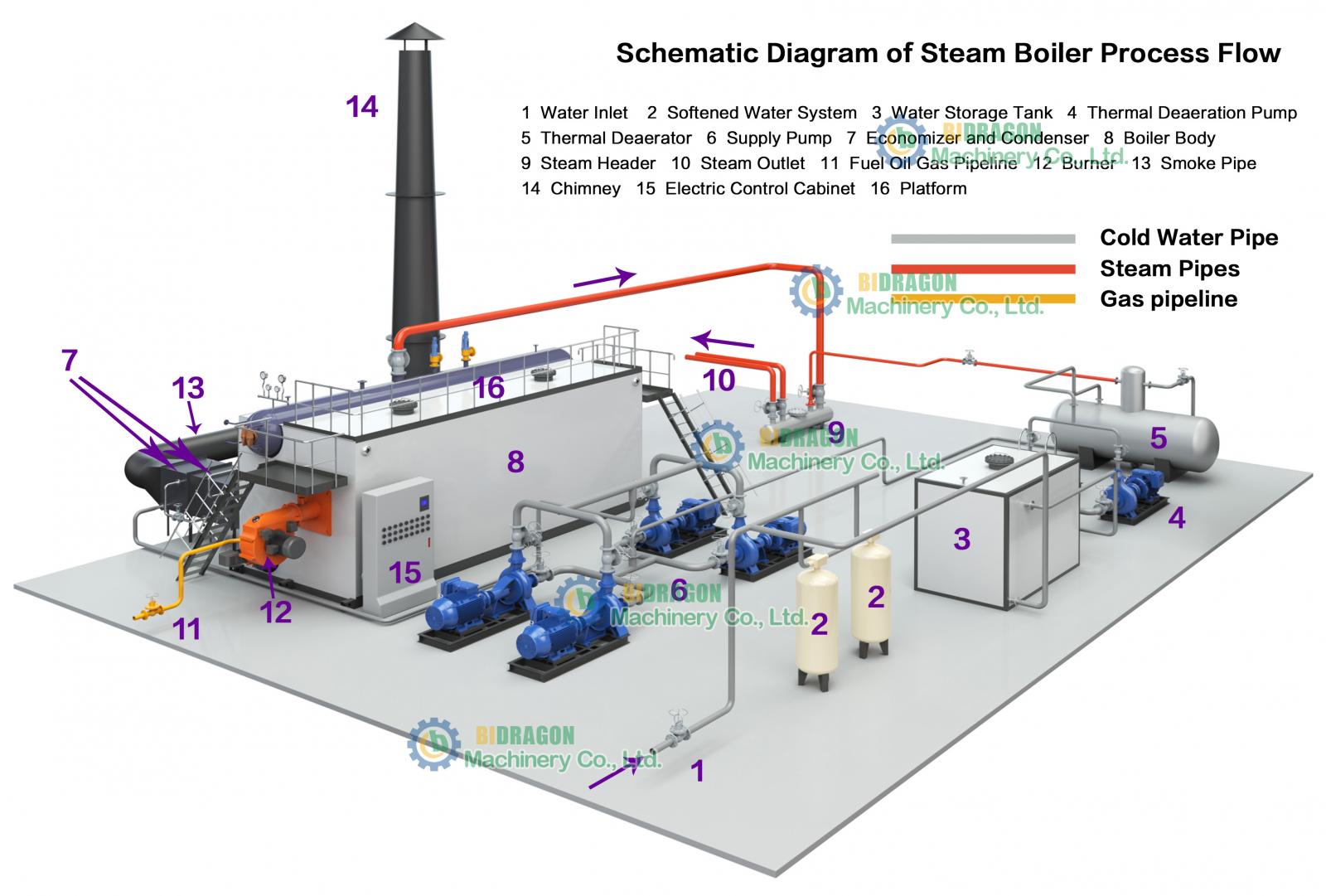
The basic function
The main task of the industrial boiler is to produce steam or hot water to provide heat for homes, commercial premises and industrial buildings. Both industrial hot water boilers and industrial steam boilers depend on fuel for their operation.
Fuel-driven heating process
When the burner is activated, the fuel (e.g., natural gas, oil, etc.) begins to burn, producing a large amount of heat. This heat is transferred to the water inside the boiler in different ways. In some boilers, the heat from the flame is allowed to transfer indirectly to the cold water through a heat exchanger; in other small boilers, the flame comes into direct contact with the water to heat it.
The way the heat is transferred
Steam boiler: In a steam boiler, water is heated into steam, and the steam relies on the pressure generated during the heating process to flow through the piping system and deliver heat to various places where it is needed.
Hot water boilers: Hot water boilers, on the other hand, with the help of a circulation pump, push the heated hot water along the piping system, allowing the heat to circulate throughout the system to heat different areas.
Water / Steam Circulation
Steam condenses into water after releasing heat, hot water decreases in temperature after dissipating heat, and this condensed or cooled water is reintroduced back to the boiler through the piping to be heated again, and so on to ensure continuous and stable heating.
Emissions
The heating process of a boiler produces a by-product - flue gases. These gases may contain hazardous substances and therefore need to be properly discharged through the chimney system and must comply with the relevant environmental regulations in order to minimize pollution to the environment.
Main Components of the Boiler
Burner
The burner is called the “heart” of the boiler, which is responsible for mixing the air with the fuel source, thus triggering combustion and providing the necessary heat for heating the fluid. Its workflow works like this: when the system needs heat, the thermostat sends an electronic signal to the burner. Fuel is then pumped into the boiler from an external source (usually an adjacent fuel tank) through a filtration mechanism. Nozzles on the burner convert the fuel into a fine spray and ignite it, which triggers a reaction in the combustion chamber.
Combustion chamber
As the name suggests, the combustion chamber is where the fuel is mixed with air and burned. Because it has to withstand high temperatures, the combustion chamber is usually made of cast iron. During the combustion process, the internal temperature can quickly rise to hundreds of degrees Celsius. This combustion process is extremely rapid and the heat generated by combustion is transferred to the heat exchanger of the boiler.
Heat exchanger
The heat exchanger is a key component of the boiler and its role is to transfer heat between two fluids (usually water and gas) while avoiding mixing of the two substances. The heat exchanger transfers the heat generated by the burner to the water in the system, much like boiling water in a pot, where the heat is transferred from the bottom of the pot to the water in the pot, but the pot does not allow the fire to come into direct contact with the water. Heat exchangers can be made from a variety of materials, such as steel tube bundles, cast iron, or copper tubing. These materials must be robust and able to withstand high temperatures to ensure long-term use and efficient heat transfer. In the heat exchange process, high-temperature gas and cold water enter separately and come out as low-temperature gas and hot water, and the whole heat transfer process is completed without any contact between the two substances.
Other components
Water thermostat: The water thermostat sends the correct signal to the burner according to the temperature of the fluid in the boiler, decides when to start or stop the heating process, and ensures that the temperature of the water is maintained in the right range.
Check Valve: The check valve is like a safety guard, allowing the fluid to flow in one direction only, preventing backflow of fluid and ensuring safe operation of the system.
Circulation pump: The circulation pump is responsible for pushing hot water through the supply piping to the radiators or other distribution lines, which plays a key role in the normal operation of the boiler system, and good maintenance can ensure that the system works efficiently.
Control System: The control system allows the user to set the water temperature, air and fuel supply mixing ratio, internal pressure and ignition. It regulates the firing frequency of the burner, the quality of the fuel-oxygen mix, the rate of fuel consumption and the heating temperature of the water, and is an important part of the boiler safety system.
Deaerator / Condenser: The deaerator is used to remove oxygen and other dissolved gases from the liquid, while the condenser is a heat exchanger that removes latent heat from the exhaust gases so that the exhaust gases can be pumped back to the boiler after condensation. Deaerator and condenser tanks are used only in steam boiler systems, not in hot water and thermal oil boilers, where the fluid remains liquid. These two types of tanks are almost identical in construction, but have different functions. Their design is based on two main principles: thermal principle and vacuum principle.
Thermal principle: Tanks using the thermal principle are connected to the atmosphere and are usually used in small plants. Here, steam is used to maintain the tank water temperature at around 105°C to remove air from the water.
Vacuum Principle: In the vacuum principle, a jet pump creates a vacuum inside the tank, causing the water in the tank to boil due to the low temperature, thus removing the air from the water. This principle is commonly used in steam turbine applications.
Coal economizer: The coal economizer is a heat exchanger installed in the boiler exhaust vent or the ship's main engine exhaust stack. Depending on the installation location, the requirements for the pump vary greatly.
Exhaust Chimney: The exhaust chimney, also known as a flue or chimney, is responsible for safely venting the exhaust gases from combustion to the outside of the building. It may be a traditional brick chimney or a series of metal pipes. Exhaust chimneys must be constructed safely and securely to ensure that dangerous gases such as carbon monoxide are vented away from the interior of the building, taking care not to vent exhaust gases near doors and windows, and also to prevent strong winds from backing up back into the commercial premises.
Expansion tank: This small tank takes on the important responsibility of protecting the boiler from excessive pressure, ensuring safety throughout the operation.
Supply piping: In a circulating heating system, the supply piping is responsible for transporting the heated hot water or steam to the various distribution points and conveying the thermal fluid flow to the distribution points in the boiler.
Refractories: Refractories are used to fill any gaps or openings that may exist around the furnace chamber, ensuring that the flame is centered in the chamber for improved combustion efficiency and safety.
Return Pipes: As the water cools or steam cools back to liquid water, the return pipes bring this water back to the boiler to be reheated, creating a complete cycle.
Superheater: The superheater is an important part of the boiler and is installed in the path of the hot flue gas discharged from the furnace. It uses the heat in the flue gas to superheat the steam before it enters the turbine, and its main purpose is to increase the temperature of saturated steam without increasing the steam pressure.
The Type of Boiler
Electric boiler
Electric boilers utilize electricity to generate heat and are a popular choice for those who do not have access to natural gas supply. It is efficient, compact and easy to install, making it particularly suitable for sites with limited space.
Natural gas boilers
Natural gas boilers are the most common type of boiler. It generates heat by burning natural gas, which is cost-effective and relatively environmentally friendly. Due to its efficiency and reliability, it is widely used in various types of buildings.
Steam boiler
Steam boilers generate steam by heating water and then use the steam cycle to supply heat. Due to their high heating capacity, they are commonly used in industrial applications. However, steam boilers require careful monitoring and maintenance to ensure optimal performance.
Condensing boilers
Condensing boilers are extremely efficient, utilizing heat from exhaust gases to preheat cold water entering the boiler, greatly reducing energy consumption and fuel costs. It is the ideal heating solution for those who seek to save energy.
Combination boiler (Combi)
The combi boiler saves space by combining the functions of a water heater and a central heating boiler in one unit. It is able to provide hot water on demand and is popular in small houses or apartments, especially suitable for living environments with limited space.
Hot water boilers
Hot water boilers are mainly used to heat water and distribute hot water to buildings to provide a heat source for heating and domestic hot water. Commonly used in large residential and commercial buildings, they can use natural gas, oil or electricity as fuel.
Oil-fired boilers
Oil-fired boilers produce heat by burning heating oil. In areas where natural gas is not available, oil-fired boilers have become important heating equipment due to their reliability and efficient energy utilization.
Application Areas of Boilers
The field of power generation
In the process of power generation, boilers are the core components of thermal power plants. First, a fuel (such as coal, natural gas or oil) is burned in the boiler chamber, generating heat that converts water into steam. The high-pressure steam drives a turbine connected to a generator, which rotates to produce electricity. The boiler, as the key to this process, provides the steam power necessary for large-scale power generation.
Heating system
Whether it is a residential, commercial or industrial building, boilers are an important part of the heating system. In residences, boilers provide hot water to homes to ensure a comfortable living environment; in commercial and industrial locations, boilers generate steam or hot water to efficiently heat large spaces. The heated water or steam passes through radiators, radiant floor heating systems or other heat exchangers to transfer warmth to all corners.
Industrial processes
Many industrial processes rely on steam generated by boilers. For example, in manufacturing, steam is used for equipment sterilization, drying, and chemical reactions. Textile, paper and food processing industries, relying on boilers to accurately control the temperature, to help a variety of production processes to ensure product quality and production efficiency.
Chemical production
Chemical plants use boilers to achieve a variety of functions. Boilers provide the necessary heat for chemical reactions and play an important role in the distillation process. It maintains the specific temperatures required for various chemical production processes. In addition, the boiler assists in the cooling process, creating ideal conditions for chemical production and guaranteeing the efficiency and stability of chemical production.
Oil refineries
Boilers are indispensable in oil refineries. Crude oil undergoes a variety of treatments before it can be converted into refined products, and the high temperature steam generated by boilers is used in distillation columns, crackers and reforming processes. Boilers are critical to maintaining specific temperatures and creating the conditions needed to refine crude oil, and are a key component in the production of refined fuels such as gasoline and diesel.
Mining
Boilers are used for a variety of purposes in mining operations. At remote mining sites, steam from boilers is often used to generate electricity. Meanwhile, during ore processing, high-temperature steam is used in leaching, smelting and refining. In addition, in cold climates, boilers provide heating for mining facilities, ensuring a suitable working environment and guaranteeing efficient and stable mining operations under complex conditions.
The Summary
Through this paper, we have gained a comprehensive understanding of all aspects of boilers. From its rigorous definition, to the complex and subtle working mechanism; from the synergistic operation of various key components, to the rich and diverse types; and the wide range of applications in many fields, all highlight the importance of boilers in modern society. Whether it is to ensure the comfort of daily life, or to promote the efficient operation of industrial production, boilers play an irreplaceable role. We hope this article has inspired you to take more interest in boilers, and if you have any questions or want to explore further, feel free to delve deeper.