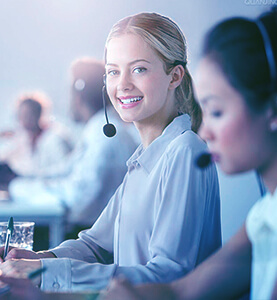
Low Pressure Steam VS. High Pressure Steam: How to Choose A Required Boiler
Introduction to Steam Boilers
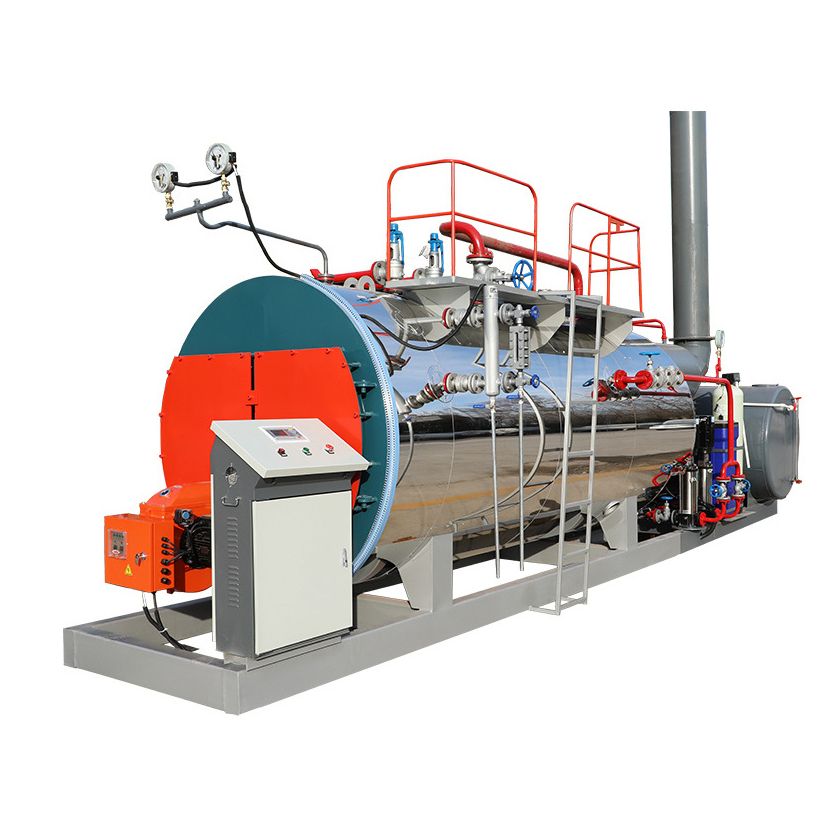
Steam boilers, an important equipment in industrial production and everyday life, can be broadly categorized into two types, high pressure and low pressure, based on pressure parameters.
Over the past 50 years, the use of steam for conventional heating (space heating) has declined as many companies have adopted newer technologies. However, specific industries such as beer brewing, distilling, dairy production, and scientific laboratories have seen an increase in the demand for steam heating and have reaped many benefits from it.
How to Define High-Pressure and Low-Pressure Steam Boilers
In the early 1900s, when boiler codes and regulations were being established, boilers operating at pressures of 15 PSI (pounds per square inch) and above were defined as high-pressure boilers, while those operating at pressures below that were categorized as low-pressure steam boilers. This standard has been used in the industry for over a hundred years, and related boiler codes and standards have been built around it. It's critical to know whether you have a high- or low-pressure boiler, as there are differences in the regulatory requirements for different types of boilers.
Every boiler pressure vessel is factory rated and stamped with the appropriate pressure rating. There is usually a data label on the boiler (usually labeled with the manufacturer's name and model number) that lists the boiler's maximum allowable working pressure (MAWP). If the label is illegible or missing, there will also be a stamping on the actual pressure vessel with a unique identifier and MAWP. If the MAWP is 15PSI or less, then the boiler is a low pressure boiler; above that, it means the boiler is defined as a high pressure boiler.
Low Pressure Steam Boilers VS High Pressure Steam Boilers
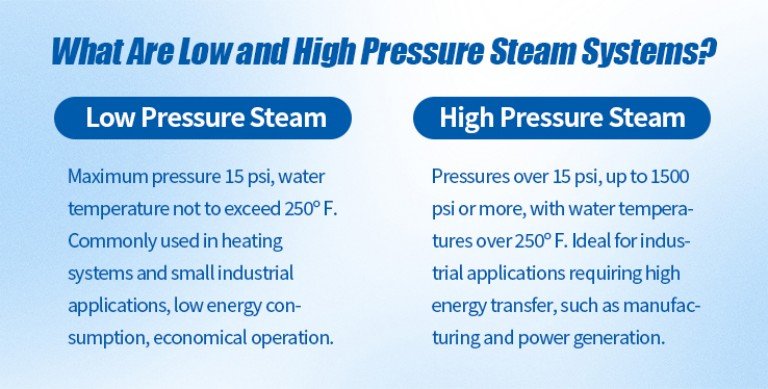
Steam Generation
Low pressure steam boilers are designed for a variety of applications such as heating buildings, driving small turbines, or powering some industrial processes. It is capable of generating steam to meet a variety of needs, whether it is for gentle space heating or for industrial operations that do not require high steam temperatures.
High-pressure boilers are capable of generating high-temperature, high-pressure steam, which leads to a significant increase in their power output. In power stations, high-pressure steam drives steam turbines, which in turn generate electricity, and is an important part of modern power production. The enormous energy contained in high-temperature, high-pressure steam can be efficiently converted into mechanical energy, which is then converted into electrical energy to meet large-scale power needs.
Safety
Because low-pressure boilers operate at lower pressure levels, the risk of catastrophic failure is usually low. Moreover, these boilers are generally equipped with safety devices to prevent excessive pressure buildup. For example, common safety valves can open automatically when the pressure exceeds the normal range, releasing excess pressure and ensuring safe boiler operation.
Heating Systems
Low-pressure boilers are widely used in heating systems in residential, commercial and public buildings. The steam generated by the boiler can be passed through radiators, convectors, or underfloor heating systems to transfer heat to individual rooms, creating a warm and cozy environment for people. This type of heating is not only efficient, but also distributes heat more evenly.
high-pressure steam boilers, In some cases, are also used in district heating systems. Through a network of pipes, steam is delivered to multiple buildings or facilities for centralized heating. This approach is more common in urban areas or large industrial complexes, and is able to unify the deployment of energy, improve the efficiency of energy use, and provide a stable supply of heat to a large area.
Industrial applications
Low pressure steam boilers also play an important role in many industrial processes. For example, in the food processing industry, can be used for food heating, cooking and sterilization; textile manufacturing industry, can assist the fabric dyeing, finishing and other processes; in pharmaceutical production, to meet the heating and drying requirements of the pharmaceutical production process; paper mills, to help the paper drying and some of the process. These applications utilize the characteristics of low-pressure steam to provide stable, moderate heat.
High-pressure steam boilers are essential equipment in industries such as chemical production, petroleum refining, steel manufacturing, and cogeneration plants. Production processes in these industries often involve intense heating operations, or require the use of steam in high-pressure environments to ensure the efficient operation of the process. For example, in chemical synthesis reactions, high-pressure steam provides the heat and pressure conditions required for the reaction; in petroleum refining, it is used for critical steps such as distillation and refining of crude oil. In the marine sector, such as steamships and naval vessels, high-pressure steam boilers provide steam for propulsion systems.
How to Choose a Required Steam Boiler?
Operating pressure and temperature
Low-pressure steam boilers operate at pressures below 15 PSI and at steam temperatures typically in the 100°C - 120°C range. These parameters make it suitable for scenarios with relatively low temperature and pressure requirements.
High-pressure steam boilers operate at pressures higher than 15 PSI and produce steam at temperatures up to 500°C or more. The high temperature and pressure of the steam gives it a powerful energy output for applications with high energy requirements and demanding process conditions.
Complexity and Maintenance
Low-pressure steam boilers have relatively simple overall structures and systems due to their low operating pressures and temperatures. This not only reduces initial equipment costs, but also makes routine maintenance much easier, with relatively infrequent and inexpensive maintenance.
In contrast, high-pressure steam boilers need to be manufactured with stronger, high-temperature and high-pressure-resistant materials due to the fact that they operate in high-temperature and high-pressure environments. Their system structure is more complex, and in order to ensure safe and stable operation, they require more frequent maintenance checks to monitor equipment wear, pressure control, etc. Maintenance costs are naturally higher.
Evaluating Business Needs
Before selecting a steam boiler, a company must thoroughly sort through its business needs as well as the actual condition of the facility. The first step is to identify what kind of steam conditions are needed for optimal production, including steam pressure, temperature, flow rate and other parameters. Only based on an accurate analysis of the needs to build a matching steam system, to avoid unnecessary costs due to improper equipment selection.
Reasonable determination of boiler size
It is critical to properly select the size of the boiler. A properly sized boiler can effectively heat a building, avoiding fuel waste and frequent boiler starts and stops. Especially for low-pressure boilers, make sure they are able to adapt to the most extreme weather conditions in your area. A boiler that is too small may not be able to meet heating needs in cold weather, while a boiler that is too large will result in wasted energy and increased costs to run the equipment.
Burner Selection
For businesses with low steam demand, a lower-cost simple atmospheric burner can be chosen. This type of burner has a simple structure and can meet the basic needs of steam generation.
For enterprises with higher steam demand, a more powerful power burner model is more appropriate, which can provide higher steam production and greater flexibility in adjusting the steam output to adapt to the changing demand for steam volume at different stages of production.
Multi-Boiler Control Systems
For companies with complex heating needs, a multi-boiler control system can be used to run large-scale production activities more efficiently. By rationally configuring the operating status of multiple boilers, the supply of steam can be precisely adjusted according to actual demand, improving energy utilization efficiency and reducing operating costs, while also increasing the reliability of the system, so that when one of the boilers breaks down, the others will still be able to maintain a portion of the production demand.
Seek Industry Expert Advice
When choosing a low-pressure steam boiler for a business, it is best to consult with an expert with specialized knowledge in the industry. Experts are able to advise on the most appropriate boiler for a company's specific steam system operational needs. They can also provide detailed information on different steam piping designs to ensure that the equipment selected is seamlessly integrated with the actual application to achieve optimal performance.
Conclusion
There are significant differences between low-pressure and high-pressure steam boilers in terms of operating pressure, temperature, application scenarios, complexity, and maintenance requirements. When choosing a steam boiler, companies must fully consider their business needs, facility conditions and future development plans. At the same time, consulting with industry experts and making decisions based on professional advice will help you select the most suitable steam boiler to ensure efficient, safe and economical operation of your production activities.