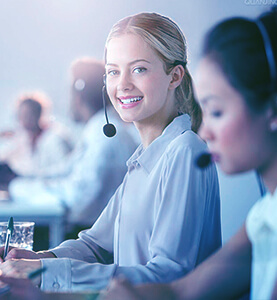
How Gas Boilers Work
Gas boilers play a pivotal role in modern industry and everyday life. From large-scale industrial production to providing warmth to thousands of homes, gas boilers have become a key piece of equipment in the field of energy conversion thanks to their high efficiency and cleanliness. So, how exactly does the gas boiler operate to realize the magical transformation from gas to heat? Next, let's take a closer look at how it works.
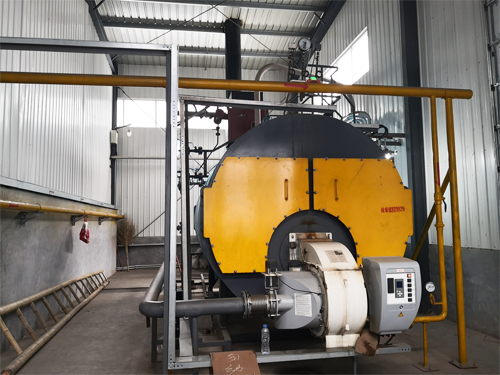
What is a Gas Boiler?
A gas boiler is a device that uses gas as a fuel to heat water and convert it to steam. At its core, it releases heat through the combustion of gas, which in turn provides energy for the production of steam.
The key role of the burner
The burner is called the “heart” of the gas boiler and bears the heavy responsibility of burning the fuel. During the combustion process, it mixes the gas with air in the proper proportion, prompting the gas to burn fully, releasing a large amount of energy, which is transferred to the water inside the boiler, driving the generation of steam.
Common gas types
Common gas fuels include liquefied petroleum gas (LPG), compressed natural gas (CNG), liquefied natural gas (LNG), and so on. Different gas appliances have unique properties, and burner manufacturers will carefully design burners to match these properties to ensure the best combustion results.
Classification of Gas Boilers
Classification by Structure
- Firetube boilers:In fire-tube boilers, high-temperature flue gases flow inside the tubes while water surrounds them outside. This structure is relatively simple, suitable for some of the steam production and pressure requirements of the relatively small application scenarios.
- Water tube boiler: In contrast to the fire tube boiler, the water in the water tube boiler flows inside the tube, and the flue gas is flushed outside the tube. It is capable of withstanding higher pressures and is suitable for large-scale industrial production where higher steam parameters are required. Manufacturers choose the structure taking into account the capacity of the boiler as well as the required steam parameters.
Classification by steam parameters
- Saturated Steam Generator:This type of boiler produces steam in a saturated state, where there is a correspondence between temperature and pressure. Saturated steam is widely used in many industrial processes that require high temperature stability, such as food processing, textile printing and dyeing.
- Superheated Steam Generator:Superheated steam generator produces steam at a temperature higher than the saturation temperature at the corresponding pressure. Superheated steam has a higher energy content, commonly used in power generation, some special chemical reactions, and other occasions requiring stringent steam quality.
Classification by fuel
- Gas boiler: purely gas fuel as energy, relatively clean combustion process, less emissions.
- Liquid Fuel Boiler:Using liquid fuel such as fuel oil, it may be chosen in some areas where gas supply is inconvenient.
- Mixed-fuel boilers: capable of burning both gaseous and liquid fuels, providing users with a flexible choice of fuel to cope with different energy supply situations.
Working Principle of Gas Boiler
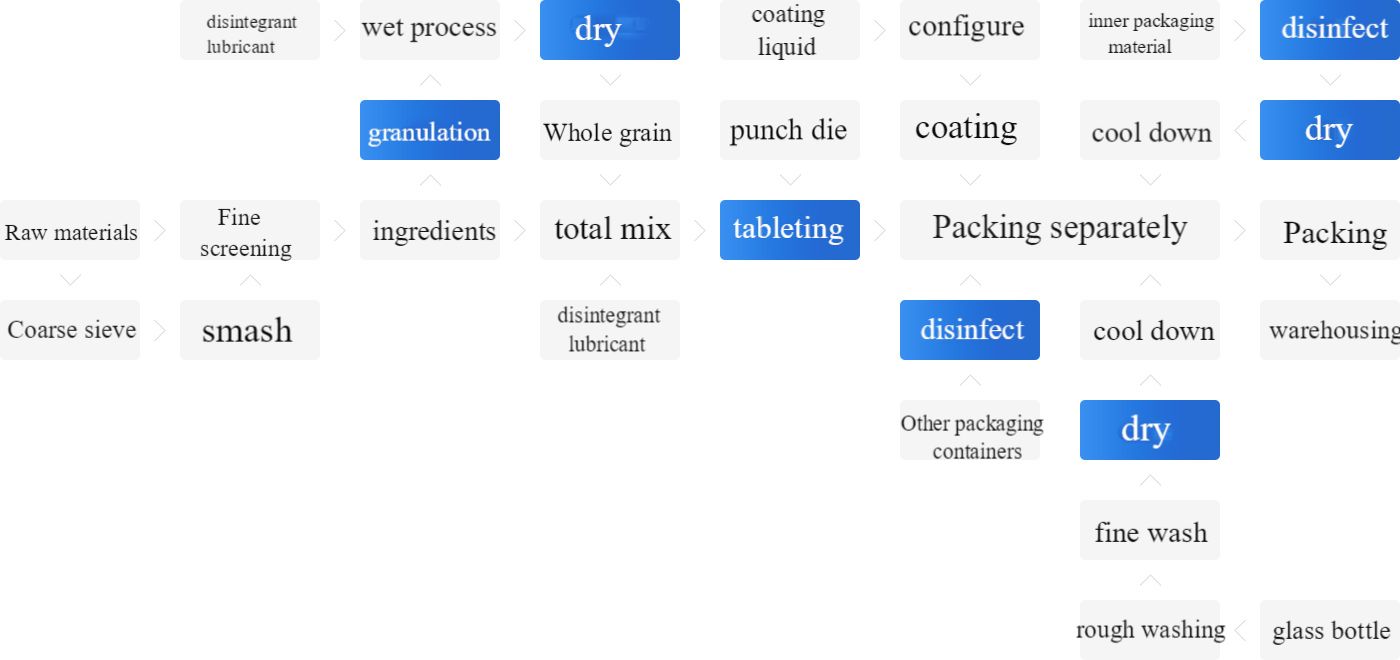
Combustion Process
- Fuel Input:Usually, natural gas or LPG is piped into the combustion chamber. This fuel is supplied at a constant pressure and flow rate within the pipeline, ensuring the continuity of the combustion process.
- Ignition start:Inside the combustion chamber, the ignition system is activated to start the combustion of the gas. This process is essentially a chemical reaction between the gas and the oxygen in the air. Hydrocarbons in the gas combine with oxygen and partially combust to produce heat, water vapor, and carbon dioxide. For example, the chemical equation for the combustion of methane (the main component of natural gas) is: CH₄ + 2O₂ → CO₂ + 2H₂O + heat.
- Efficient Combustion Guarantee:In a gas boiler, the entire combustion process must be carried out quickly and accurately to achieve efficient energy conversion. This requires a burner with precise air - fuel ratio adjustment, as well as a stable ignition and flame monitoring system to ensure that the fuel is fully burned, maximizing the use of fuel energy to provide a stable heat source for the heating system. Modern gas boilers are designed with the control and optimization of the combustion process as a key consideration, with the aim of improving thermal efficiency, reducing emissions and ensuring equipment reliability.
Heat conversion stage
- Heat Transfer: The high-temperature flame produced by fuel combustion releases a large amount of heat energy, which is transferred to the water in the boiler in a variety of ways. The first is thermal radiation, the high temperature of the flame directly to the surrounding radiation of heat; followed by thermal convection, high-temperature flue gas in the flow process will be transferred to the heat surface of the boiler; and finally, heat conduction, heat through the metal wall of the heat surface to the internal water.
- The transformation of water:after absorbing heat, the temperature of water gradually rises until it reaches the boiling point and begins to evaporate. Depending on the design and purpose of the boiler, the water is heated and converted into hot water or steam. In a hot water boiler, the water is heated to a certain temperature and then transported through the circulatory system to the area to be heated; while in a steam boiler, the water continues to be heated until it is completely converted into steam, which can be used for industrial production, power generation and other purposes.
- Energy delivery:The hot water or steam produced is then delivered to the area to be heated, such as the heating system of the building, the various processes in the industrial production process, etc., to meet the corresponding energy requirements. The whole process realizes the efficient conversion from fuel chemical energy to practical heat energy, which is the fundamental reason why gas boilers are widely used in the fields of heating, production and power generation.
Components of a Gas Boiler
Boiler body
- “Boiler” section: this section is the heated surface system that receives the heat from the high temperature flue gas and transfers it to the working fluid (water). It consists of the boiler shell, which is used to contain the water and withstand the pressure; the pot (the upper pot of a steam boiler is also known as the steam bag), which serves to separate the steam from the water and store the steam; the descending tube, which transports the water in the pot to the lower header; the header, which is used for distributing and collecting the work material; the water-cooled walls, which are arranged around the furnace chamber to absorb the radiant heat from the chamber; and the flue pipe, in which the high-temperature flue gas flows and transfers the heat; Separation device, to ensure that the steam drawn from the drum has a high degree of dryness; steam temperature regulator, to control the steam temperature in the appropriate range; sewage device, regularly discharged from the boiler impurities and dirt; steam superheater, the saturated steam is further heated to superheated steam; economizer, the use of flue gas waste heat to heat the feed water to improve boiler efficiency.
- “Furnace” part: This is the combustion system that constitutes the fuel combustion site. It contains the combustion equipment consisting of the furnace (combustion chamber), the front coal hopper, coal gate, grate (grate), slag removal plate and air distribution device. Fuel is mixed with air and burned in the furnace chamber to convert chemical energy into heat.
Boiler feedwater system
The boiler feedwater system consists of a large water tank with an accompanying water pump. The tank is responsible for collecting condensate return water and fresh make-up water from the system. When the water level in the boiler drops, the water level control system installed on the boiler detects the change and activates the pumps to transfer water from the tank to the boiler, ensuring that the boiler water level is maintained within normal limits.
Burner
The burner is the central piece of equipment in the combustion control system and provides the heat required for the boiler to convert water into steam. The ideal burner should achieve the highest degree of combustion efficiency at the lowest possible excess air factor. Its basic function is to mix fuel and air to initiate combustion. Burners can use a variety of fuels, the most common of which are natural gas, oil, propane and coal. In recent years, as environmental requirements have increased, many facilities have gradually shifted from using coal to more efficient and cleaner fuels such as natural gas.
Valves
In industries such as beer brewing, saturated steam is used at different pressures depending on the specific needs of the process. Steam is typically generated at the highest possible pressure and then regulated through valves to reduce the pressure to meet the requirements of a particular process. Valves play a role in this process by precisely controlling steam pressure and flow.
Accumulators
A steam accumulator is a steel pressure vessel with an insulating layer that stores high pressure hot water and steam inside. When steam demand is higher than the capacity of the boiler system, the accumulator can release the stored steam to meet production requirements. At lower loads, the plant can inject excess steam into the large volume of water inside the accumulator. Over time, the temperature and pressure of the stored water increases until it reaches saturation temperature at the boiler's operating pressure.
Deaerator
A deaerator is primarily used to reduce corrosion and extend the service life of steam generating boilers. It reduces the production of corrosive compounds in the steam system by lowering the levels of dissolved oxygen and carbon dioxide in the feedwater. Over time, this helps to protect the boiler and the metal parts of the entire steam system from damage and leaks caused by corrosion.
Coal saver
A coal saver is a heat exchange device that serves to recover heat from the flue gases emitted from a boiler and transfer that heat to the feedwater entering the boiler. A coal economizer is usually cost-effective because it utilizes an extended heat transfer surface. Unlike ordinary light-tube boilers, the tubes of a coal economizer usually have fins or coils attached to the outside of the tubes, which significantly increases the heat transfer area and improves the efficiency of heat transfer with very little additional space and tubing.
Control panel
The boiler control system assists in generating hot water or steam in a regulated, efficient and safe manner. Combustion and operation controls regulate the rate of fuel use as required. The primary operation control monitors the hot water temperature or steam pressure and sends signals to control the combustion rate, which is the rate at which fuel and air enter the burner. Common burner combustion sequences include on/off, high/low/off, and modulating controls, which are used to ensure that the boiler operates consistently according to actual demand.
Combustion chamber
The combustion chamber is where the fuel reacts with the air and generates heat to produce steam. In order to improve the efficiency of the combustion chamber, it needs to be adequately insulated to prevent heat loss through radiation and to ensure that as much heat as possible is used to heat the water in the boiler.
Boiler level gauges
Although a boiler level gauge does not directly control any equipment per se, it can immediately indicate to the operator whether the boiler water level is normal and in a safe condition so that the operator can take timely action. The American Society of Mechanical Engineers (ASME) specifies that the water level gauge is the direct reading method for determining the water level in the boiler drum, and it is critical to the safe operation of the boiler.
Chimney
A chimney, also known as a flue, is a pipe used to vent the hot combustion exhaust gases produced by a boiler to the outdoors. Usually, this pipe is made of steel. However, in condensing boilers, where the exhaust gases contain corrosive condensate, it is necessary to use stainless steel to make the chimney to prevent the pipes from corroding.
Drain tank or cooler
Steam boilers require periodic drain operations to remove solids, oil, and other undesirable substances from the boiler and to test the low water cutoff. According to International Plumbing Code 701.7, the boiler drain temperature must be below 60 degrees Celsius (140 degrees Fahrenheit). This is because if high temperature condensate is allowed to enter the drain line, it may cause deformation or damage to the pipe.
Operation Process
The natural gas steam boiler, for example, utilizes an advanced internal combustion three-way construction. This structure effectively reduces the exhaust temperature and improves heat utilization efficiency and thermal efficiency.
Fuel atomization and combustion
The natural gas is atomized through the burner, followed by the formation of a flame that fills the entire corrugated hearth. In this process, the fuel is fully mixed with air to achieve efficient combustion and release a large amount of heat.
Flue gas flow path
High-temperature flue gas flows along the furnace chamber to the return combustion chamber and then into the first tube bundle (second return). In the forward flue chamber, the flue gas turns 180 degrees and enters the second bundle (third return). Finally, the flue gases pass through the backward flue chamber into the chimney and are discharged into the atmosphere. During this process, the heat of the flue gas is continuously transferred to the water inside the boiler, realizing the efficient use of energy.
Applications of Gas Boilers
Power generation
In the power generation industry, gas boilers are a fundamental part of a cogeneration plant. First, a fuel (e.g. natural gas) is burned in the boiler chamber and the resulting heat converts water into steam. This high-pressure steam drives a turbine connected to a generator to rotate, which in turn produces electricity. It can be said that the gas boiler is the heart of the entire power generation process, providing the steam power essential for large-scale power generation.
Heating system
Residential heating: In residential houses, gas boilers provide warm hot water for families and create a comfortable living environment indoors through radiators or floor heating systems.
Commercial and industrial heating:In commercial buildings and industrial plants, the steam or hot water produced by gas boilers is also used to heat large spaces. Whether in shopping malls, office buildings or factories, gas boilers can efficiently meet the heating demand.
Industrial Production Process
Sterilization of equipment: In the food, pharmaceutical and other industries, production equipment needs to be strictly sterilized, gas boilers produce high temperature steam to meet this demand, to ensure that the production environment is hygienic and safe.Drying process:in the textile, wood processing and other industries, the product needs to be dried, the heat of the steam can accelerate the evaporation of water to improve drying efficiency.
Chemical reaction heat supply:in chemical production, many chemical reactions need to be carried out at specific temperatures, gas boilers provide a stable heat source to meet the heat demand of these reactions.
Chemical Processing
Chemical reaction heat supply: All kinds of chemical reactions in chemical plants often have harsh temperature requirements, and gas boilers can provide accurate heat to ensure the smooth progress of chemical reactions.
Distillation process: in petrochemical and other fields, distillation is an important means of separating mixtures, gas boilers produce steam for the distillation process provides the necessary heat.
Refineries
In refineries, gas boilers play a vital role. Crude oil needs to go through a series of complex processes before it can be transformed into a variety of refined products. High-temperature steam from gas-fired boilers is used in distillation columns, crackers and reforming processes to maintain specific temperature conditions and ensure that crude oil can be refined into valuable fuel products such as gasoline and diesel.
Mining
Power Generation:In remote mining areas, gas-fired boilers can be used to generate electricity to support mining equipment and production facilities.Ore Processing:During ore processing, high temperature steam can be used in leaching, smelting and refining to help extract useful mineral components.
Facility Heating: In cold regions of the mine, gas boilers provide heating for mining facilities, ensuring a suitable working environment for staff and the smooth running of mining operations.
Conclusion
The gas boiler realizes the efficient conversion from gas to heat energy through the unique combustion process and heat energy conversion mechanism. Its diverse classification, complex composition structure and wide range of applications make it an indispensable energy equipment in modern industry and life. Whether in power generation, heating or industrial production, gas boilers continue to play a key role in providing stable energy support for the development of society and people's lives. We hope that through this article, you have a deeper understanding of the working principle of gas boilers. If you have other questions about gas boilers or need further technical advice, please feel free to contact us.