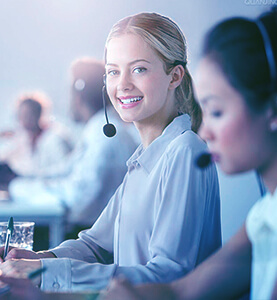
How Does Industrial Steam Boiler Work?
Industrial steam boilers play a vital role in today's industrial sector. Whether it's a large manufacturing process or an energy supply industry, industrial steam boilers play an integral role in providing the necessary power to support a variety of industrial activities. In this article, we'll take an in-depth look at how industrial steam boilers work, their core components, how they are categorized, how they are heated, what they require in terms of maintenance, and the wide range of industrial applications they are used for.
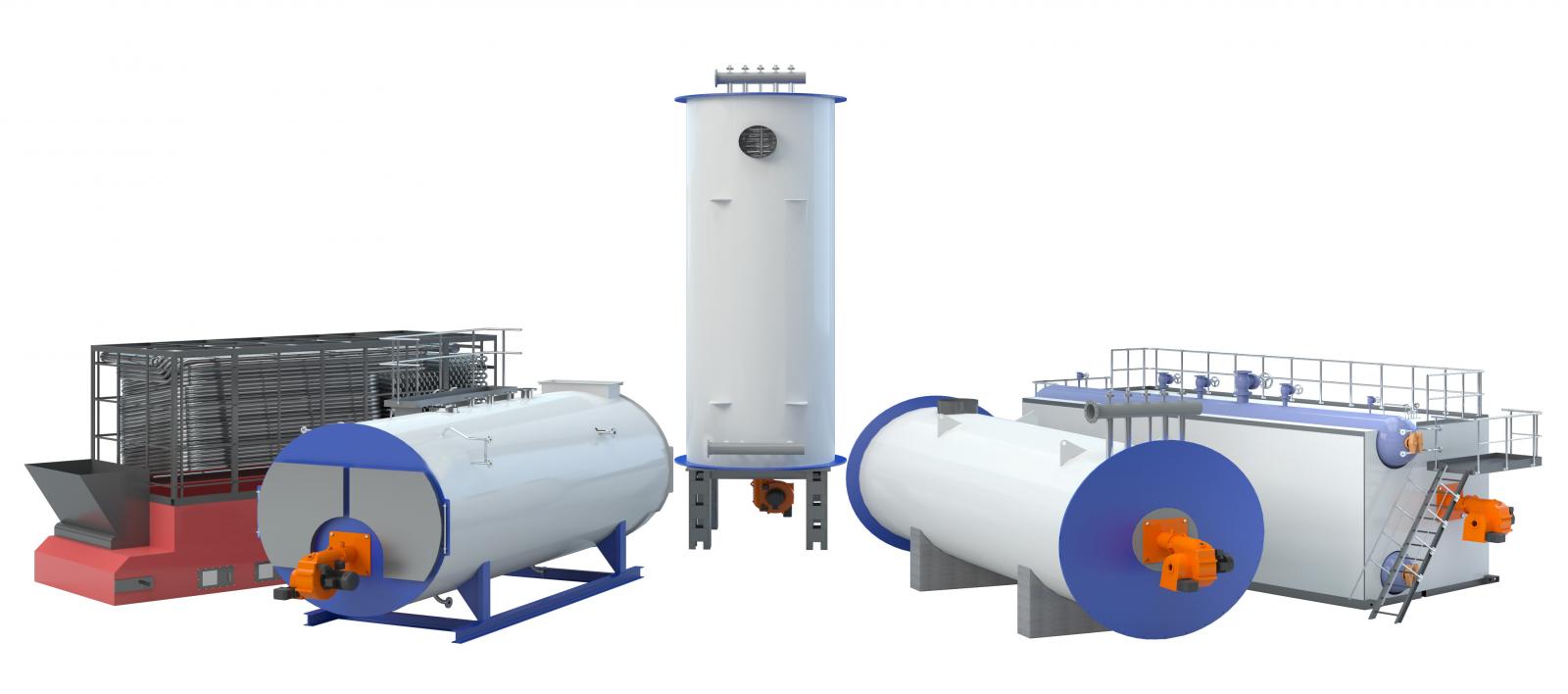
Basic Principles of Operation
The basic working principle of an industrial steam boiler is to produce pressurized steam by heating water to the boiling point through a combustible fuel source. The heating method is mainly categorized into two types: fire tube boilers and water tube boilers.
In a fire tube boiler, the combustible fuel source is located in a tube surrounded by water. The heat generated by the combustion of the fuel is gradually transferred to the surrounding water through the walls of the tubes, and as the heat builds up, the water is heated to boiling, ultimately producing steam. This type of boiler is relatively simple in structure and is suitable for a number of industrial scenarios where the steam demand pressure is low and the load is small.
Water tube boilers work in a different way. In this type of boiler, water is contained in multiple tubes and the heat generated by the fuel source is applied to the outside of the tubes. When the hot flame and hot gases come in contact with the outer walls of the tubes, the heat is quickly transferred to the water inside the tubes, which is heated and boiled into steam. Water tube boilers are able to withstand higher pressures and heat loads and are commonly used in large-scale industrial production and power generation.
Core Components
Industrial steam boilers consist of several core components, each of which plays a unique and critical role in the steam generation process.
Pressure Vessel
The pressure vessel is an important part of an industrial steam boiler, and is used to contain gases or liquids at high temperatures and pressures. During boiler operation, the pressure vessel is subjected to tremendous pressure, so it is often manufactured using high-strength materials, such as steel, to ensure its safety and reliability.
Burner
The main function of a burner is to provide heat to the boiler by burning fuel and oxygen. Common fuel sources include natural gas, low-pressure propane, No. 2 oil, coal, and others. Different fuels have different combustion characteristics, and the burner will be designed and adjusted accordingly to the type of fuel used to achieve efficient combustion and stable heat output.
Tubes
In a water tube boiler, metal tubes hold water on the inside and receive heat from the burning fuel on the outside. These tubes are usually made of special steel to withstand high temperatures and pressures, ensuring that the water can be safely and efficiently heated and converted into steam.
With a fire tube boiler, the hot gases from combustion are passed through the tubes, which transfer the heat to the water that surrounds them, allowing the water to be heated and steam to be produced. The design and layout of the tubes affects the heat transfer efficiency and steam production of the boiler.
Coal Saver
A coal economizer is a heat exchange device that serves to recover heat that would otherwise be lost in the exhaust gases and use that heat to preheat the water entering the boiler. In this way, the economizer reduces the additional energy required to heat the incoming water, significantly improving the boiler's energy efficiency and reducing operating costs.
Deaerator Tank
A deaerating tank is a pressurized feedwater tank that uses pressure and heat to remove oxygen and other dissolved gases, especially carbon dioxide, from the water entering the boiler. Dissolved oxygen and carbon dioxide in the water can cause serious corrosion of the boiler, and the presence of a deaerating tank effectively protects the metal parts of the boiler and extends the service life of the boiler.
Heat Exchanger
The heat exchanger acts as a heat transfer in the boiler, transferring the heat from the hot gases to the water in the boiler while ensuring that the two substances do not come into direct contact. This indirect heat transfer improves the safety and efficiency of heat transfer and is one of the key components for efficient boiler operation.
Control Panel
The control panel allows the operator to control the operating parameters of the boiler, such as temperature and pressure. In commercial and industrial boilers, control panels are often equipped with detailed analytics to monitor the boiler's operating status in real time, providing data such as fuel consumption, steam production, and thermal efficiency to help the operator make timely adjustments to the operating parameters to ensure stable and efficient boiler operation.
Feedwater Tank
The feedwater tank is a container for storing and supplying the water used by the boiler to generate steam. Treated water is first collected in the feedwater tank and then pumped to the boiler. Chemicals that remove oxygen and protect boiler metals are often added to the feedwater tank to ensure that the water entering the boiler meets requirements. In addition, some facilities with condensate return systems can collect and return the condensate from the cooling of the steam to the feedwater tank, allowing for the recycling of treated water.
Combustion Systems
Combustion systems generate heat by mixing air and fuel and igniting them. Ensuring the correct ratio of air to fuel is critical to the proper operation of the combustion system. If the air-to-fuel ratio is not correct, it may result in inadequate combustion, producing large amounts of pollutants while reducing the thermal efficiency of the boiler. For this reason, combustion systems are often equipped with a precise air-fuel ratio control system to ensure efficient, clean combustion.
Reverse Osmosis Systems
Reverse osmosis systems utilize high pressure pumps to increase the pressure on the raw water side, forcing the water through a semi-permeable membrane, which leaves approximately 95% - 99% of the dissolved impurities in the water on the concentrated water side, allowing for deep purification of the water entering the boiler. The water treated by the reverse osmosis system effectively reduces the risk of scaling and corrosion inside the boiler and improves the operational stability and service life of the boiler.
Chemical Monitoring System
The chemical monitoring system accurately monitors chemical levels within the boiler and provides continuous analysis. By carefully controlling the amount of chemicals added, chemical monitoring systems optimize boiler operation, preventing scale formation, reducing corrosion, and ensuring that the quality of steam meets the requirements of industrial production.
Classification of Boilers
Water Tube Boilers
As mentioned earlier, in a water tube boiler, water flows inside the tubes while hot combustion gases surround the tubes. This design allows water tube boilers to withstand high pressures and heat loads, making them suitable for large-scale industrial production and power generation where high steam quality and output are required.
Fire Tube Boiler
Fire tube boilers, on the other hand, have hot combustion gases flowing inside the tubes, surrounded by water. Fire tube boilers are simple in structure and low in cost, and are suitable for small industrial enterprises or some auxiliary production processes with relatively low requirements for steam pressure and output.
Natural Circulation
Natural circulation boilers utilize the density difference of water to achieve water circulation. During boiler operation, heated water decreases in density and flows upward, while cooler water is denser and flows downward, resulting in natural water circulation. This type of circulation does not require additional power equipment and has lower operating costs, but requires higher structural design and installation of the boiler.
Forced Circulation
Forced circulation boilers circulate water through the boiler by means of a pump. This type of circulation allows for more precise control of the flow rate and speed of water circulation, and is suitable for industrial applications that require higher steam production and quality, and where the load varies greatly.
Stationary Boilers
Stationary boilers are mainly used in power plants and other locations that require a steady, large supply of steam. They are usually installed in a fixed location and have a large capacity and high steam parameters to provide continuous, efficient power support for power generation equipment.
Portable Boilers
Portable boilers are characterized by their mobility and are often used in temporary workplaces, such as construction sites and field operations. They are small in size, easy to install and dismantle, and can quickly provide steam service where it is needed.
Horizontal Boiler
The main components of horizontal boilers are placed horizontally, and this layout makes the boilers relatively small in terms of floor space, which is suitable for industrial plants or places with limited space. At the same time, the structural design of horizontal boilers facilitates the full combustion of fuel and the even distribution of heat.
Tilting Boiler
Tilting boilers are installed at a certain angle, and this design is advantageous in some specific industrial applications, such as when gravity needs to be utilized to assist certain processes (e.g., slag removal), tilting boilers are better able to meet the production requirements.
Low Pressure Boilers
Low pressure boilers produce steam at pressures up to 15 - 20 bar and are mainly used for heating purposes, such as heating industrial plants, and certain production processes that require low temperature steam.
Medium Pressure Boilers
Medium pressure boilers produce steam at pressures ranging from 20 - 80 bar, and are commonly used in power generation. In some small power plants or industrial captive power stations, medium-pressure boilers generate electricity by generating steam that drives a turbine to provide power to the business or surrounding area.
High Pressure Boilers
High-pressure boilers produce steam at pressures in excess of 80 bar, and are commonly used in large power plants and industrial processes that require extremely high steam quality and parameters, such as certain chemical processes.
Subcritical Boilers
If a boiler produces steam at a pressure below the critical pressure, it is called a subcritical boiler. Subcritical boilers are still widely used in the modern power industry, and their operating parameters and technical characteristics are between medium pressure and supercritical boilers.
Supercritical Boilers
Supercritical boilers are capable of producing steam at pressures higher than the critical pressure. This type of boiler has higher thermal efficiency and lower pollutant emissions, and is one of the important technical means for modern large-scale power plants to pursue efficient and clean power generation.
Pressurized Fuel Boiler
A pressurized fuel boiler uses a special method to pressurize fuel and feed it into the furnace chamber, which improves the combustion efficiency of the fuel and increases the heat output of the boiler. The pressurized fuel boiler has obvious advantages in some industrial production where the steam output and thermal efficiency are very high.
Pulverized Coal Fuel Boiler
Pulverized coal fuel boilers pulverize coal into a fine powder and feed it into the furnace for combustion. The combustion of pulverized coal enables the fuel to mix well with the air to achieve a more efficient combustion process, increasing the thermal efficiency of the boiler while reducing the emission of pollutants.
Method of Heating the Boiler
Steam boilers heat water by absorbing the heat generated by combustion, and heat transfer is mainly realized by three methods: radiation, convection and conduction.
Radiation
Radiation is the process of energy transfer through electromagnetic waves emitted by all elements and objects. In a steam boiler, radiant heat emitted by the flame in the combustion chamber is absorbed by the tubes. The efficiency of radiant heat transfer depends on the rate of absorption of electromagnetic waves by the surface of the object. The material and surface characteristics of the tubes affect their ability to absorb radiant heat; for example, tubes with rough surfaces are better able to absorb radiant heat, thereby increasing the efficiency of heat transfer in the boiler.
Convection
Convection is the phenomenon of heat transfer within a liquid or gas caused by density differences due to uneven heating. When a liquid or gas is heated, its density decreases and it becomes lighter, thus rising, while the colder, denser liquid or gas replenishes it. In a steam boiler, the heated water or gas rises and the cooler portion falls, creating a continuous cycle of heating and mixing. This convection process helps to distribute heat evenly inside the boiler and improves the efficiency of heat transfer.
Conduction
Conduction is the process of heat transfer through direct contact between the surfaces of objects. In metals, heat can be transferred quickly through the vibration of atoms. In a steam boiler, when the outer wall of a tube is heated, heat is conducted through the tube wall to the inner wall, which in turn heats the cold water inside the tube. The thermal conductivity of the tube plays a key role in the efficiency of conduction, and tubes are usually manufactured from metals with good thermal conductivity to ensure efficient heat transfer.
Fuel Type
Different boilers use different fuel sources to generate heat.
Gas Boilers
When a gas boiler receives a command to heat from a thermostat, it ignites the gas and oxygen in the combustion chamber by means of an ignition device, such as a small flame or an electric starter. The gas is fully combusted in a safe combustion chamber, producing a large amount of heat. This heat warms up the heat exchanger (which usually consists of copper piping), which in turn transfers the heat to the water flowing through it. Gas-fired boilers are one of the most common types of boilers available and are widely used in both industrial and residential applications due to their relatively low installation and operating costs.
Oil-fired Boilers
An oil-fired boiler works in a similar way to a gas-fired boiler in that the fuel oil is burned in a combustion chamber, releasing heat that heats a heat exchanger, which in turn heats the water. However, the main difference between oil-fired boilers and gas-fired boilers is that the fuel needs to be stored in specialized tanks and needs to be replenished regularly. In addition, oil-fired boilers are relatively less environmentally friendly, but in some cases, depending on the model, their thermal efficiency may be higher than that of gas-fired boilers. Overall, however, oil-fired boilers typically cost more to operate than gas-fired boilers due to the volatile and relatively high price of fuel oil.
Electric Boilers
Electric boilers are usually used in locations where natural gas is not available. Unlike oil and gas boilers, electric boilers generate heat through an electric heating element. When an electric current is passed through the heating element, the element heats up and transfers the heat directly to the surrounding water. While the combustion process is cleaner, electric boilers have higher operating costs due to the relatively low efficiency of converting electrical energy into heat, and in large-scale industrial applications, they require higher stability and capacity of the electrical power supply.
How to Maintain a Steam Boiler
Steam boilers require regular maintenance to ensure their safe and efficient operation. Maintenance programs typically include the following tasks:
Cleaning the Boiler
Regular boiler cleaning is an important part of maintenance. Over time, deposits such as scale and soot can build up inside the boiler, and these deposits can affect the efficiency of heat transfer and reduce the performance of the boiler. With specialized cleaning tools and methods, these deposits can be removed, restoring the heat transfer efficiency of the boiler and reducing energy consumption.
Check Boiler for Leaks and Damage
Regularly inspecting your boiler for leaks and damage is key to ensuring its safe operation. Inspections include the piping, valves, connections, and other parts of the boiler for steam leaks, water leaks, or other signs of damage. Any problems found should be repaired in a timely manner to prevent leaks and damage from expanding further and avoid potential safety incidents.
Replace Worn or Damaged Parts
During long-term operation of the boiler, some parts may become damaged due to wear and tear, corrosion, and other reasons. Timely replacement of these worn or damaged parts can ensure the normal operation of the boiler and avoid production interruptions caused by component failure. Maintenance personnel should regularly check the wear and tear of key components and replace them as appropriate.
Test Boilers for Leaks and Damage
In addition to daily inspections, boilers need to be thoroughly tested on a regular basis to detect potential leaks and damage issues. Commonly used testing methods include pressure testing and non-destructive testing. Pressure testing checks the sealing and structural integrity of the boiler under pressure by applying a certain amount of pressure to the boiler; non-destructive testing utilizes a variety of technical means (e.g., ultrasonic testing, radiographic testing, etc.) to detect the presence of internal defects without damaging the boiler's structure.
Industrial Applications of Steam
Steam plays an important role in many industrial processes.
Driving Industrial Processes
Steam-powered equipment is widely used to drive production in numerous factories. Steam can directly power machines, such as in some textile and paper mills, where steam-driven engines run the machines to complete the production process. In addition, steam can be used to heat materials, provide heat for production processes that require high temperature environments, or provide compressed air to assist in the operation of power equipment.
Industrial Heating Applications
Steam is used in a wide range of industrial heating applications. On the one hand, it is used to heat buildings to provide a comfortable working environment in industrial plants. On the other hand, in many industrial production processes, such as food processing and chemical production, where precise temperature control is required, steam can provide a stable and efficient heat source to meet the temperature requirements of different processes.
Cleaning and Sterilization
In industrial environments, steam is used to clean and sanitize surfaces and equipment. High-temperature steam can effectively remove dirt, bacteria and viruses, and is particularly suitable for industries with high hygiene requirements, such as pharmaceuticals and food and beverage processing. Steam cleaning is not only efficient, but also environmentally friendly and does not produce environmental pollution as some chemical cleaners do.
Cooling and Refrigeration
In some industrial applications, steam can also be used for cooling and refrigeration processes. Through a vapor compression refrigeration cycle or absorption refrigeration cycle, steam enables heat transfer for cooling and refrigeration purposes. For example, in some large data centers, steam refrigeration systems are utilized to cool servers and ensure proper operation of equipment.
Conclusion
Industrial steam boilers provide vital steam power for industrial production through a complex and subtle working mechanism. From its basic working principles, to the synergistic functioning of its many core components, to the different classifications, heating methods, fuel types, and stringent maintenance requirements, each of these components is closely interconnected and works together to ensure the boiler's efficient and safe operation.
The widespread use of steam in the industrial sector also further highlights the importance of industrial steam boilers. With the continuous progress of science and technology, the future of industrial steam boilers are expected to achieve higher efficiency in the design and operation of the boiler, lower emissions and stronger intelligent control, for the sustainable development of industry to provide more powerful support.