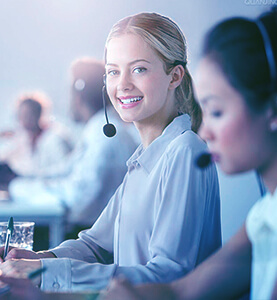
What Are The Common Problems With Biomass Fired Boilers?
What Are The Common Problems With Biomass Fired Boilers?
Introduction
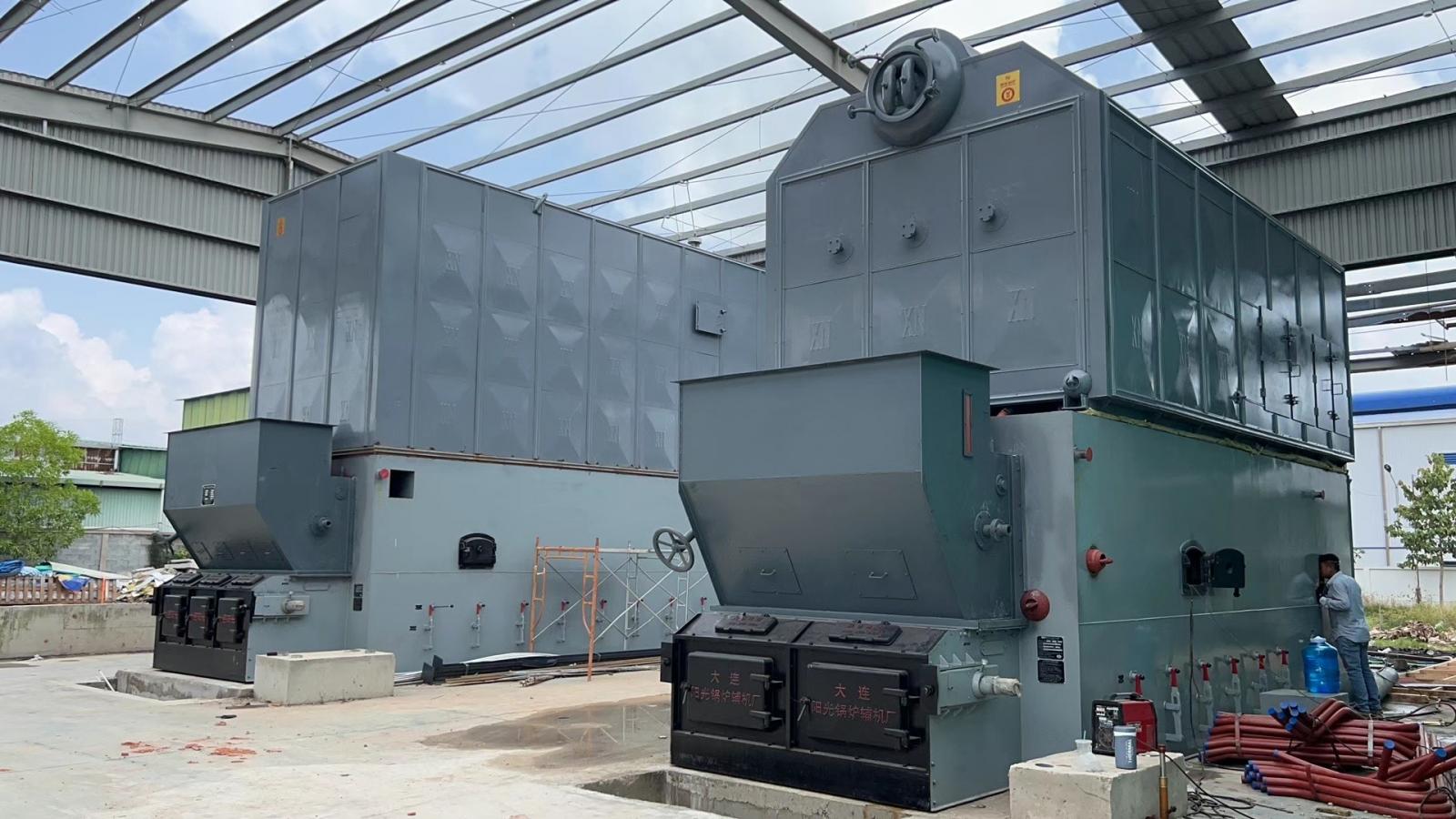
Biomass boiler, as a kind of equipment utilizing renewable biomass fuel to generate heat or electricity, occupies an important position in the industrial and energy field. It not only helps to reduce the dependence on traditional fossil fuels, but also significantly reduces carbon emissions, making a positive contribution to the cause of environmental protection. Next, let us explore the biomass boiler in the practical application of the problems that often occur and their response.
What is a biomass boiler?
Biomass Boiler Definition
Biomass steam boiler is a kind of equipment that converts the chemical energy in solid biomass fuels into heat energy, and the heat energy it generates can be used for power generation or heating for industrial production process. Through clever design, it realizes the efficient conversion of biomass to usable energy.
Components and Types
Heat exchange body : This is one of the core components of the biomass boiler. In the heat exchanger body, the high temperature gas from combustion flows and transfers the heat it carries to the water circulating in it, which is heated and converted into steam. Steam serves as an important energy carrier for a wide range of industrial needs.
Types of boilers: In the case of boilers manufactured by Bidragon, there are three main types. Fire-tube boilers, characterized by high-temperature flue gases flowing inside the firetube, where heat is transferred through the walls of the firetube to the water outside; water-tube boilers, where heat is exchanged between the water flowing inside the watertube and the flue gases flushing outside the watertube; and fire-tube boilers, which are a combination of firetube and watertube, with the choice of one type or the other depending on the characteristics of the fuel. Different fuels, such as particle size, moisture content, combustion characteristics, etc., are suitable for different types of boilers to ensure optimum combustion and heat transfer efficiency.
Combustion technology: Biomass boilers can use a variety of combustion technologies. Among them, the stepped grate technology through the stepped design of the grate, so that the fuel is fully combusted at different stages; the lower feeding feeding technology feeds the fuel into the combustion chamber from the lower part to ensure the continuity and stability of the fuel supply; the fluidized bed technology makes use of the fluidized medium to make the fuel combust rapidly under the fluidized state, which has the advantages of high combustion efficiency and strong adaptability.
Fuel Types of Biomass Steam Boilers
Biomass steam boilers are able to use a wide variety of fuels, which is also one of its major advantages. Common fuels include virgin wood, wood chips, bark, industrial waste wood (B and C grade wood), olive pomace, grape pomace, coffee pomace, chicken manure, straw, sanding dust, olive kernels, oversized pellet compost, almond shells and sawdust. The design of the boiler is closely related to the type of fuel used.
There are differences in the physical and chemical properties of different fuels, such as calorific value, moisture content, and volatile content. These properties determine the combustion method and combustion effect of the fuel, so when designing the boiler, the fuel factor needs to be fully considered to ensure that the boiler can operate efficiently and stably.
How a Biomass Boiler Works
The working principle of a biomass boiler is relatively intuitive and easy to understand. Biomass fuels, such as common wood pellets, wood chips or agricultural waste, are fed into the combustion chamber of the boiler through a specialized conveying system. Inside the combustion chamber, the fuel burns vigorously at high temperatures and in an environment with plenty of oxygen, releasing a large amount of heat energy. This heat energy is transferred through the heating surface of the boiler to the water or other heat transfer medium in the boiler, which is heated to a high temperature steam or hot water state. Biomass fuels are widely available and renewable, and the carbon dioxide produced during the combustion process can be absorbed by plants, creating a natural carbon cycle, which not only reduces the negative impact on the environment, but also effectively lowers greenhouse gas emissions. In addition, some advanced biomass boilers are even able to use challenging materials such as vegetable oils and animal fats as fuel, further broadening the range of biomass applications.
Common Operational Problems of Biomass Boilers
Mechanical Wear
Causes of Wear
Thermal Stress: biomass boilers experience frequent heating and cooling cycles during operation. This drastic change in temperature causes thermal stresses within the metal parts. Long-term exposure to this thermal stress will gradually change the crystal structure of the metal parts, leading to a reduction in their strength and the appearance of cracks or deformation.
For example, the combustion chamber wall of the boiler, the heated tube and other parts, due to direct contact with high temperature flue gas, the temperature change is the most obvious, so the damage caused by thermal stress is also the most prominent. ·
Abrasive particles: biomass fuels produce ash and other residual particles during the combustion process. These particles are usually hard and angular, and driven by the high temperature flue gas, will be at a high rate of scouring the metal surfaces inside the boiler. Prolonged scouring will gradually wear down the metal surfaces like sandpaper sanding, thinning the components and reducing their service life.
For example, parts such as flue and superheater are prone to wear problems due to long-term erosion of ash particles in the flue gas. ·
Insufficient lubrication: There are many moving parts inside the boiler, such as the bearings of the fan and the transmission parts of the feeding system. If these parts are not adequately lubricated, a large friction will be generated between the surfaces in contact with each other. Friction not only consumes additional energy, but also accelerates the wear and tear of components.
For example, a long-term lack of lubrication of fan bearings will lead to wear of the bearing surfaces, which in turn will affect the normal operation of the fan and may even lead to fan failure.
Preventive Maintenance Strategies
Inspecting Critical Components: Regular inspections of the boiler's critical components are an important means of detecting wear and tear problems in a timely manner. For example, conduct weekly or monthly visual inspections of components such as combustion chamber walls, heating tubes, fan bearings, etc., to see if there are any cracks, deformation or signs of surface wear.
Cleaning the boiler: Timely removal of ash and other residue from the inside of the boiler is critical to minimizing wear and tear. You can regularly use compressed air or specialized cleaning tools to blow and clean the combustion chamber, flue, heating surface and other parts.
Lubricate moving parts: select high-quality lubricants and regularly lubricate the moving parts of the boiler in accordance with the requirements of the equipment manufacturer. During the lubrication process, ensure that the lubricant is evenly applied to the contact surfaces of the parts to form an effective lubricating film and reduce friction.
Monitoring operating parameters: Paying close attention to the boiler's operating parameters, such as temperature, pressure, and flow rate, can help to detect potential problems in a timely manner. For example, by monitoring the temperature changes in the combustion chamber, you can determine whether the combustion is normal; by monitoring the steam pressure, you can understand the boiler's output. If abnormal fluctuations in operating parameters are found, they should be immediately investigated to find out the causes and take appropriate measures to adjust them.
Ash accumulation problem and its impact on boiler efficiency
How ash accumulation hinders heat transfer
Ash accumulation is one of the common problems in the operation of biomass boilers, and its impact on boiler efficiency should not be ignored. Studies have shown that the thermal efficiency of a boiler may be reduced by as much as 20% when ash buildup is severe. This means that more fuel needs to be consumed to obtain the same heat output, which increases operating costs.
Effective ash accumulation removal techniques
Manual cleaning: For mild cases of ash accumulation, manual cleaning is a simple and effective method. Operators can use tools such as wire brushes and scrapers to clean the ash accumulation area directly. In the cleaning process, pay attention to the strength and angle to avoid scratching the heat transfer surface.
Soot blower: Soot blower is a device that uses compressed air or steam to remove accumulated ash. It can be in the boiler operation process, regularly to the heat transfer surface of the high-pressure air or steam jet, will accumulate ash blowing down. The advantages of the soot blower are that it enables automated operation, saves labor, and can be cleaned without affecting the normal operation of the boiler.
Chemical cleaning: When ash buildup is more stubborn and difficult to remove by physical methods, chemical cleaning methods can be considered. Chemical cleaners are able to react chemically with the components in the ash buildup, making it loose and easy to remove. In the use of chemical cleaners, according to the material of the boiler and the nature of the ash to choose the appropriate cleaner.
Frequent sewage Discharge: Regularly discharging accumulated ash from the bottom of the boiler is one of the most important measures to prevent ash accumulation problems. By draining the boiler frequently, large particles of ash can be removed from the boiler in a timely manner, reducing their deposition on heat transfer surfaces.
Incomplete Combustion Issues
What is Incomplete Combustion
Incomplete combustion is a phenomenon in which a biomass boiler fails to fully combust fuel during operation. Ideally, biomass fuels should be combusted in such a way that all chemical energy is completely converted into heat energy while producing a minimum of by-products. However, in actual operation, due to various factors, the combustion process may not be able to reach the ideal state, resulting in the occurrence of incomplete combustion. Incomplete combustion brings a series of problems. First, some of the fuel will be underutilized, resulting in a waste of resources. Secondly, incomplete combustion produces harmful gases such as carbon monoxide (CO), volatile organic compounds (VOCs) and particulate matter, which are not only polluting to the environment but also hazardous to human health. In addition, incomplete combustion also reduces the thermal efficiency of the boiler, so that the heat generated per unit of fuel is reduced, increasing energy consumption and operating costs.
Reasons for Incomplete Combustion
Insufficient Oxygen: Adequate oxygen supply is indispensable for the full combustion of fuel. In a biomass boiler, a proper air - fuel ratio needs to be maintained to ensure a smooth combustion reaction. If the amount of air entering the combustion chamber is insufficient, the combustible components of the fuel will not be able to come into full contact with oxygen, resulting in incomplete combustion. ·
Poor quality of fuel: The quality of fuel has a significant impact on the combustion effect. If the moisture content of biomass fuel is too high, during the combustion process, the moisture needs to absorb a lot of heat in order to evaporate, which will reduce the combustion temperature of the fuel and make combustion difficult.
In addition, uneven size of fuel particles can also affect the uniformity of combustion. Larger particles may not be able to burn fully in a short period of time, while smaller particles may be quickly carried out of the combustion chamber by the airflow, resulting in inadequate combustion. Moist wood chips or straw, for example, will have significantly reduced combustion performance. ·
Improper boiler settings: The operating parameter settings of the boiler, such as combustion temperature, combustion time, and burner adjustment, play a key role in combustion performance. If the combustion temperature is too low, the fuel cannot reach the activation energy required for full combustion, and the combustion reaction will be incomplete.
In addition, improper adjustment of the burner, such as the angle of fuel injection, uneven injection amount, etc., will also lead to uneven mixing of fuel and air, thus triggering incomplete combustion.
Biomass Boiler Inefficiency Problems
Lack of annual maintenance : Maintenance of biomass boilers at least once a year is crucial to ensure their efficient operation. If maintenance is not performed for a long period of time, various deposits will gradually accumulate inside the boiler, such as ash from combustion, incompletely burned fuel particles, and impurities.
These deposits will form a thick layer of cover on the heat transfer surface, greatly impeding the transfer of heat from the burning fuel to the circulating water.
Poor combustion: poor combustion is one of the main causes of inefficiency in biomass boilers. As mentioned earlier, incomplete combustion prevents the fuel from fully releasing its energy, resulting in a large amount of wasted energy.
Solving the problem of poor combustion requires a multifaceted approach, such as adjusting the air-fuel ratio, optimizing burner settings, and improving fuel quality. Only by ensuring that the combustion process is adequate and stable can the energy efficiency of the boiler be improved.