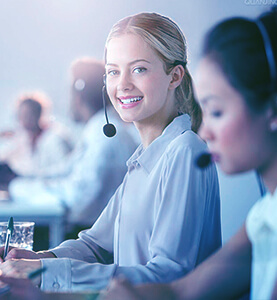
8 Types Of Industrial Steam Boilers
A steam boiler is a system that generates steam by heating water, the core function of which is equivalent to a heat exchanger that converts water into steam for external applications. Industrial steam boilers play an integral role in many industrial sectors. Steam boilers provide a critical source of power and heat to support production in a wide range of industries.
There are many different types of industrial steam boilers, each with its own unique design, principle of operation, application scenarios, as well as advantages and disadvantages. Next, we'll take an in-depth look at several common industrial steam boiler types, including fire tube boilers, water tube boilers, industrial electric steam boilers, waste heat boilers, condensing steam boilers, shell boilers, combination boilers, and biomass boilers.
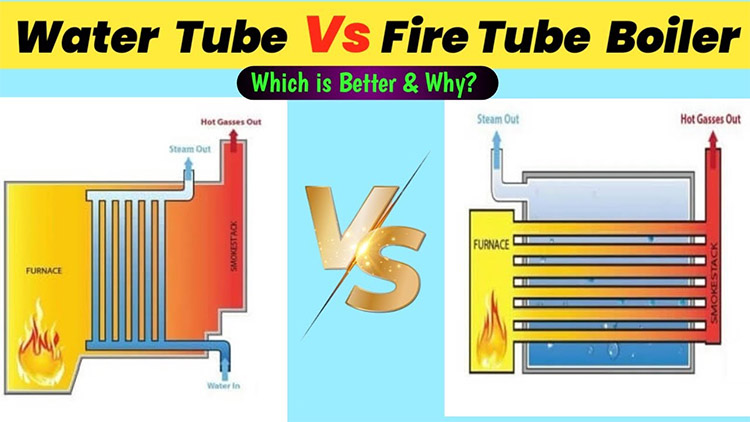
Fire Tube Boiler
The fire tube boiler is one of the most basic and long-established boiler designs. In this type of boiler, a burner injects a flame into a tube (i.e., a firetube) that is submerged in the water inside the boiler's main vessel. There may be more than one fire tube. The heat from the flame is transferred to the water through the firetube, heating the water to the boiling point. Below are the different classifications of fire tube boilers.
- Horizontal Return Firetube Firetube Boiler: In this configuration, a large steam drum is mounted horizontally within the shell and support structure. Multiple fire tubes extend from the furnace chamber and are similarly arranged horizontally within the drum. Because the drum is horizontal, the fire tubes are submerged by water when the drum is filled with water. This design allows for efficient heat transfer from the fire tubes to the water.
- Short Firebox Firetube Boilers: Short firebox firetube boilers have a relatively short firebox construction and are designed for efficient combustion and heat transfer in a limited space. This type of boiler is suitable for small industrial applications where space is a limitation, but a steady supply of steam is still required.
- Compact Firetube Boiler: The compact firetube boiler utilizes a compact layout design that rationally combines individual components to reduce overall size. It takes up less space while maintaining a certain level of steam production, making it ideal for sites with limited space.
- Horizontal Fire Tube: The internal chamber design of the Horizontal Fire Tube allows the fire tube to be arranged horizontally inside the chamber. This layout helps to heat the water inside the tubes evenly and improves heat transfer efficiency, making it suitable for industrial production processes that require a certain level of steam quality and output.
- Vertical Fire Tube Boilers: Vertical fire tube boilers have fire tubes mounted vertically in the furnace chamber. This configuration allows for a smoother upward path for water and steam, and can perform well in specific industrial applications, such as certain small-scale processes that require rapid steam generation.
Water Tube Boiler
Water tube boilers work in a very different way to fire tube boilers. In a water tube boiler, the flame and hot combustion gases flow outside the tubes while water circulates inside the tubes. Fuel is burned in the furnace chamber and part of the water tubes usually form the furnace wall.
A water tube boiler operates in a simple water tube circuit where a bubble of steam forms on the heated side of the tube. The resulting vapor-water mixture is less dense than the cooler water on the unheated side, and thus rises, creating a cycle through the system. The steam bubbles continue to rise until they reach the steam drum, where the steam is separated from the water and enters the steam space.
In a naturally circulating water tube boiler, water circulates between the steam drum at the top and the mud drum at the bottom due to density differences. The heated water becomes a vapor-water mixture and becomes less dense, flowing upward into the steam drum, while the cooler water is denser and flows downward back into the mud drum, thus creating a natural cycle.
In forced circulation boilers, the water is circulated by pumps. The pump is able to more actively control the circulation path and flow rate than a circulation pattern based solely on density differences. This is important for boilers operating over a wide range of capacities, as it ensures stable, efficient operation under varying load conditions.
Watertube boilers are commonly used in electric utilities and large manufacturing sites where large capacity or high pressure steam is often required. Most watertube boilers are built on-site, although smaller “turnkey” units are now available. With the advantages of easy installation and a short construction period, a complete water tube boiler is a good choice for companies that do not have a particularly high demand for steam and want to get up and running quickly.
Industrial Electric Steam Boiler
Industrial electric steam boilers are powered by electricity and, unlike other types of boilers, do not involve the transfer of combustion energy. Its design utilizes both vertical and horizontal boiler shell orientations.
Industrial electric steam boilers can be used for both steam and hot water systems. For example, in places with high environmental requirements where combustion exhaust emissions are not allowed, such as certain laboratories and electronic production workshops, industrial electric steam boilers are able to take advantage of their ability to provide clean steam and hot water.
Electric steam boilers have the following very obvious advantages
High regulation ratio: it can flexibly adjust the steam output in a wide range to adapt to different demand for steam. For example, in the production process, according to the changes in the process, the steam output can be adjusted quickly and accurately.
Zero emission: Since no combustion process is involved, no harmful gas emissions such as carbon dioxide and sulfur dioxide are produced, which is very friendly to the environment.
Thermal shock resistance: better resistance in the face of rapid changes in temperature, higher stability of the equipment, reducing the risk of failure due to thermal shock.
However, high-capacity industrial electric steam boilers require a large amount of installed power. Currently, available electricity has become a limiting factor for the wide application of this technology. However, related fields have been pushing for innovation, and it is expected that high-capacity, sustainable industrial electric steam boilers will be realized in the near future, providing efficient and clean steam and hot water solutions for more industries.
Waste Heat Boiler
Waste heat boilers effectively capture excess heat from industrial processes or exhaust gases and convert it into useful steam. In many industrial processes, a large amount of otherwise wasted heat is generated, and the presence of a waste heat boiler allows this heat to be recovered and utilized.
Waste heat boilers transfer waste heat from industrial processes to the water in the boiler through a specific heat exchange structure, causing the water to be heated and evaporate to produce steam. For example, in the steel production process, when high-temperature waste gas passes through a waste heat boiler, the heat it carries is absorbed by the boiler and steam is produced.
This not only significantly reduces fuel consumption and cuts down on operating costs, but also improves energy efficiency, making it a cost-effective and environmentally friendly solution. By recovering waste heat, companies can reduce their dependence on additional fuel and lower their energy procurement costs. At the same time, the direct emission of heat is reduced, and thermal pollution of the environment is reduced accordingly.
Waste heat boilers are widely used in industries such as cement, steel and glass manufacturing as well as power plants. In these energy-intensive industries, the recovery of waste heat is critical to improving overall operational efficiency. For example, in cement plants, waste heat boilers can utilize the waste heat from the exhaust gases emitted from the cement kiln to generate steam, which can be used to generate electricity or for other production processes, thus realizing the gradual utilization of energy.
Condensing Steam Boiler
Condensing steam boilers are rapidly gaining favor in the industrial and residential markets. In domestic and small industrial applications, condensing hot water boilers are able to achieve efficiency levels (90% or higher) not possible with other standard boilers due to the relatively low temperature of the hot water circuit.
Condensing steam boilers are equipped with a specially designed heat exchanger that lowers the flue gas temperature sufficiently to condense the water vapor in it. During this condensation process, additional heat is released which is captured and reused. For example, the heat released during the condensation process is transferred to the cold water entering the boiler by means of special piping and heat exchanger structures that raise the preheating temperature of the cold water, thus reducing the amount of energy required for heating.
In this way, the condensing steam boiler maximizes the use of energy and improves the overall thermal efficiency of the boiler. It not only saves energy costs, but also reduces fuel consumption and exhaust emissions, which also has positive significance for environmental protection.
Shell Boiler
The heat transfer surface of a shell boiler is enclosed within a steel shell. It employs a number of different pipe layouts which affect the number of times heat is transferred through the system until it is finally discharged. Also known as a flue boiler, a shell boiler has a long cylindrical tank and uses fire tubes. Heat from the furnace or combustion chamber passes through these fire tubes to heat the water.
The earliest boiler of this type was the Cornish boiler, which featured a long cylinder with a single, large flue or tube to contain the heat or flame. It was later replaced by the Lancashire steam boiler, which featured two flues for the flame. The structural improvements in the Lancashire steam boiler allowed for more efficient heat transfer and the ability to produce more steam, meeting the growing demand for steam from the industrial development of the time.
The shell and tube steam boiler, also known as the shell and tube boiler, is one of the simplest boiler designs and is known for its efficient and economical steam production. Its relatively simple construction and low maintenance costs, as well as its ability to provide a steady amount of steam, make it suitable for industrial production scenarios where the demand for steam is not particularly huge and where cost-effectiveness is sought.
Combination Boiler
A combination boiler is a newer type of boiler that combines the functions of a boiler and a hot water storage tank. This means that it can heat water directly from the mains without the need for a separate hot water storage tank. In a domestic hot water supply system, a combi boiler is able to instantly heat cold water to provide a constant supply of hot water according to the user's water needs.
A combi boiler is more energy efficient than a conventional boiler. This is because it avoids the problem of heat dissipation from traditional hot water storage tanks, reducing energy wastage. At the same time, since there is no need to install an additional hot water storage tank, the combi boiler takes up less space, which is a great advantage for places with limited space, such as small apartments and compact commercial stores.
Biomass Boiler
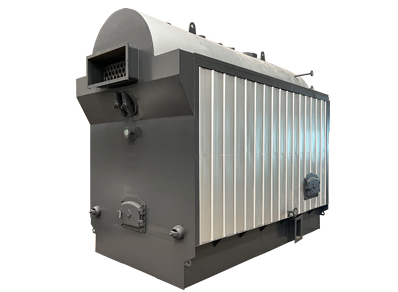
Biomass boilers are designed to burn organic materials such as wood, agricultural residues and even specially grown energy crops. These organic materials release heat during combustion, which powers the boiler. Biomass fuels are renewable compared to traditional fossil fuels.
The use of biomass fuels as an energy source helps to reduce dependence on fossil fuels, lower carbon emissions and is more environmentally friendly. Moreover, in some areas with abundant agricultural resources, biomass fuels are relatively easy to obtain and may be less costly. For example, in the vicinity of wood processing factories, waste wood trimmings can be used as fuel for biomass boilers, enabling the recycling of resources.
Biomass boilers are commonly used in industries with abundant biomass resources, such as wood processing and agriculture. In wood processing plants, a large amount of wood waste can be directly used as fuel for biomass boilers for heating, drying and other production processes. In the agricultural field, agricultural residues such as crop residues can also be converted into heat by biomass boilers to provide energy support for agricultural production and rural life.
Conclusion
Industrial boilers play a vital role in a wide range of industries, providing the necessary heat, steam and power to support production processes. From chemical to food processing, textile to power generation, the stable operation of industrial boilers is one of the key factors in ensuring normal production in various industries.
Understanding the different types of industrial boilers and their application scenarios is essential for companies to choose the right boiler for their specific needs. The right choice can significantly impact the efficiency, safety and overall productivity of an industrial process.
As technology continues to advance, the industrial boiler industry continues to evolve. In the future, we can expect to see even more efficient and sustainable boiler solutions.